- Comment
(0)
Comparison: 10 renowned Chinese injection molding machine brands (Part 1)
Different brands of injection molding machines offer unique competitive advantages and technologies. Selecting the right injection molding machines involves more than just considering the price.
In this article, Adsale Plastics Network presents a comparison of 10 renowned Chinese injection molding machine manufacturers, each varying in size and expertise. We examine their history, network, clamping force range, product series, and technological advantages. This overview is designed to help you quickly grasp essential information.
10 renowned Chinese manufacturers to know
1. Chen Hsong Group
Brand: Chen Hsong
Established year: 1958 (listed in Hong Kong in 1991)
Headquarters: Hong Kong, China
Production and service network: Chen Hsong Group has multiple facilities in China, including locations in Taiwan Taoyuan, Guangdong Shunde, Shenzhen, and Zhejiang Ningbo. Among these, the Chen Hsong Industrial Park in Shenzhen and the facilities in Shunde serve as the Group’s main manufacturing and R&D centers.
Chen Hsong has established branches in Europe, South America, and India, with its European headquarters located in the Netherlands and a subsidiary in Germany. In South America, it has set up an integrated display center and a spare parts center. Chen Hsong injection molding machines are sold in many countries around the world, including the US, Canada, France, the UK, Brazil, Argentina, Mexico, and most Southeast Asian countries.
Revenue (2023-2024): HKD 2.01 billion
Annual productivity: Approx. 20,000 units
Machine clamping force: 65,000 kN (max.)
Major applications: Automotive, Packaging, E&E
Flagship series: MK6 series, SPARK series, Two-platen injection molding machines
MK6 series includes PRO, PLUS, and MAX versions. MK6 PRO is equipped with precise toggle, patented mold plate, high-precision injection unit, linear guide, precise hydraulic oil circuit, and other advanced hardware and intelligent control systems. MK6 large servo injection molding machine features innovative design in clamping unit, injection unit, and other components. With optimized software for control system and oil circuit, the machine achieves high efficiency in large product manufacturing.
Chen Hsong MK6 PRO series servo injection molding machine.
SPARK series offers both all-electric and hybrid machines. The all-electric version integrates hardware such as a precision electric motor, linear guide, patented mold plate, and specialized screw, along with software like an ultra-speed intelligent controller and highly sensitive sensors. The hybrid version is equipped with precision hydraulic system, intelligent electric controller, precision electric motor, and other advanced hardware and software.
Chen Hsong two-platen injection molding machine is designed for high performance, precision, and repeatability. Its robust stability minimizes downtime and reduces maintenance needs.
Technology and product advantages: With over 60 years of industry experience and innovation, Chen Hsong injection molding machines leverage advanced overseas technology to achieve exceptional precision, speed, and stability. These machines integrate mechanical design with a focus on safety, ensuring high accuracy even during extended high-speed operations.
Chen Hsong machines utilize closed-loop fast dynamic control technology, enabling smooth and shock-free mechanical motions that minimize wear on components. The advanced controller features adaptive intelligence, allowing for prompt compensation of misaligned parts, thus maintaining stable and precise performance.
The cutting-edge two-platen technology from Chen Hsong combines the company’s expertise with technology from Mitsubishi Corporation. The two-platen injection molding machine provides the largest opening stroke and daylight, delivering high precision, stability, and speed while ensuring optimal mold protection with a minimal footprint.
Developed by a team of Japanese technical experts, Chen Hsong’s “Non-Stop” technology significantly reduces annual downtime to as low as 0.5%. This technology is initially available on the second generation of two-platen machines, with plans for integration into other models.
In addition, Chen Hsong machines feature “Precision Hydraulics” technology that eliminates overshoots and fluctuations in hydraulic circuits, even at high speeds, ensuring high and consistent product quality.
2. Fu Chun Shin Group
Brand: Fu Chun Shin (FCS)
Established year: 1974 (listed in Taiwan in 2004)
Headquarters: Tainan, Taiwan
Production and service network: Apart from Taiwan, Dongguan, Ningbo and Qianwan New Area, FCS Group has established production facility in India. The Group has also set up more than 70 sales branches in 28 countries.
Revenue (2023): RMB 1 billion
Annual productivity: Approx. 5,700 units
Machine clamping force: 60-40,000 kN
Major applications: Automotive, 3C electronics
Flagship series: FB/GW/HB-R multi-component machines
FB/GW/HB-R Multi-component injection molding machines feature servomotor to control rotary table, shortening rotary time by more than 50%. The highly efficient double servo power system is certified with the first grade of national power saving standard (≦0.40kw h/kg). The patented rotary table offers fixed and accurate positioning to extend the mold’s service life. The 5th generation of FB series launched in 2024 has been optimized to meet higher expectation.
FCS FB-R series rotary table two-component injection molding machine.
∎ Appearance: The newly designed appearance maintains the original high quality and durability. The machine dimensions are optimized for 15% less space.
∎ Clamp: The overall rigidity of the new clamping unit is improved by 15%. The rotary table is upgraded with the mold load increased by 10%. The clamping unit is equipped with linear guide, and the contactless design of movable platen and the tie bar enhances the speed of mold opening and closing by 15%.
∎ Injection: Hydraulic seat adopts linear rail structure for advance and retreat, resulting higher control accuracy. The injection unit equipped with linear guide saves energy by 10%.
∎ Controller: Comprehensive system upgrade and optimized user interface lead to higher accuracy, 20% faster reaction speed, and higher energy efficiency.
Hot seller: FB/GW/HB-R series
Technology and product advantages: Since the first generation of two-color injection molding machine was developed in 1984 and launching machine of the same type for producing pen in China in 2003, FCS Group has been a leader in the two-color machine market. The Group also completed R&D for three-color machine. When it comes to two-color injection molding machine, people will first think of FCS Group.
In view of the increasing market demand for single-color standard injection molding machine, FCS Group will constantly increase its investment in such area. With its large factory scale and location advantages, the production facility in Qianwan New Area will officially launch a product line of single-color standard machine with distinctive features and high cost-effectiveness.
Moreover, FCS Group has followed the trend of Industy 4.0 and developed iMF 4.0 (intelligent ManuFactory), an intelligent control system for manufacturing management. The system can be mounted on injection molding machines, and it can independently adjust and control quality parameters based on the surrounding information. It can also give advanced warning.
FCS Group has a comprehensive portfolio of injection molding machines, from hydraulic servo, fully electric, two-color and two-platen to specialized (such as thin wall packaging, barrel, blood collection tubes, PET preform and PVC). The machines have neat structure and offer high stability, durability and energy efficiency.
The Group’s production facilities house a wide range of precise processing equipment to produce machine parts. Machine parts have one-year warranty while structure casting parts are with two-year warranty.
3. Haitian International
Brand: Haitian, Zhafir
Established year: 1966 (Haitian International was listed in Hong Kong in 2006)
Headquarters: Ningbo, Zhejiang Province
Production and service network: As a leading enterprise in the plastic injection molding equipment industry, Haitian International has the largest plastic machinery production base in the world. The company has established six global regional management centers located in Germany, Turkey, Mexico, India, Singapore, and Japan, along with five major overseas manufacturing bases in Serbia, Mexico, India, Malaysia, and Japan.
Haitian International has also set up application experience centers in several countries and collaborates with over 60 sales and service partners worldwide. This extensive network enables the company to deliver high-quality products and services to customers in more than 130 countries and regions.
Revenue (2023): RMB 13 billion
Annual productivity: 56,000 units (max.)
Machine clamping force: 400-88,000 kN
Major applications: Haitian International owns two distinct brands: Haitian, which specializes in servo-hydraulic injection molding solutions; and Zhafir, which focuses on all-electric injection molding solutions. Their products are extensively used across various industries, including automotive, home appliances, logistics, packaging, 3C, and medical.
Flagship series: Haitian Mars series (MA), Haitian Jupiter series (JU), Zhafir Venus series (VE)
Haitian MA series servo-hydraulic injection molding machine is Haitian International's best-selling model, with over 410,000 units sold globally. Now upgraded to fifth-generation technology, the MA series features Haitian's latest self-developed servo drive system and an electric pre-molding device. It incorporates multiple energy-saving technologies, achieving a 20-40% increase in overall energy efficiency. Additionally, the machine is equipped with Haitian's intelligent ecosystem technologies, which help reduce operating costs and enhance production efficiency.
Haitian MA5 series servo-hydraulic injection molding machine.
New fifth-generation Haitian JU series servo-hydraulic two-platen injection molding machine builds on nearly 30 years of Haitian's R&D in two-platen technology. It features a space-saving design, offering a compact structure, a small footprint, and large mold space. The machine also integrates various energy-saving technologies along with Haitian's intelligent ecosystem technologies.
Zhafir VE series all-electric solution has been upgraded to fifth-generation technology, delivering advanced solutions for high-precision and high-quality injection molding. The injection molding machine features a compact structure and a stable molding process. Its standout characteristic is its smart technologies, which include the latest smart anti-interference EMC technology and anti-drift technology, enabling ultra-high precision molding. The new generation of smart mold protection can promptly detect load deviations during the mold closing process.
Hot seller: Haitian MAV/h servo-hydraulic high-speed packaging machine, Zhafir ZE series
Technology and product advantages: The two brands under Haitian International each have their own strengths. Haitian specializes in hydraulic machines that are stable and reliable, making them suitable for a wide range of general applications. On the other hand, Zhafir focuses on electric machines designed for high-end applications, emphasizing precision, cleanliness, and efficient production.
Haitian International's injection molding solutions feature highly integrated, intelligent modular designs that prioritize low maintenance costs for efficient production. The machines are equipped with multiple smart functions that enhance efficiency while meeting customized and flexible production requirements.
The company’s newly upgraded energy-saving and information technologies further optimize the injection molding process, making injection molding more energy-efficient and effective.
In addition, Haitian International has established manufacturing centers in key markets worldwide, boasting large-scale manufacturing capabilities. The core components of the machines are produced in-house, ensuring controllable quality and delivery cycles.
Over the years, the exceptional product quality and global service network of Haitian and Zhafir brand injection molding machines have become key reasons customers choose Haitian International products.
4. KraussMaffei
Brand: KraussMaffei
Established year: 1838
Headquarters: Munich, Germany
Production and service network: KraussMaffei operates a total of 16 production facilities in the world. Since 2018, KraussMaffei has invested EUR 200 million to build four factories in Germany and China, including one in Einbeck (near Göttingen), Germany and one in Jiaxing, China. The Jiaxing plant is also the company’s only regional headquarters with comprehensive functions outside Germany.
Revenue (2023): RMB 6.031 billion
Machine clamping force: 250-55,000 kN
Major applications: Automotive, Packaging, Medical, E&E
Flagship series: precisionMolding, powerMolding, PX series
precisionMolding series electric machines feature high-precision injection molding system to control injection volume and pressure, guaranteeing size and quality of the end products. The series is suitable for high-precision applications, including electronics and medical equipment.
powerMolding series hydraulic machines feature higher clamping force to ensure that the mold is completely sealed and avoid material leakage. This also ensures product quality, especially for large and structurally complex products, such as automotive parts and large plastic containers.
The all-electric PX series is designed for more flexibility while increasing productivity. The optimized clamping unit design and ejector with a large stroke allow maximum platen parallelism and more flexibility for mold use. The APCplus control technology compensates for fluctuations in the manufacturing process. Lower investment costs thanks to modular design.
KraussMaffei PX series all-electric injection molding machine.
Technology and product advantages: Injection molding machines from KraussMaffei feature adaptive process control, intelligent control, and high energy efficiency.
Adaptive process control is achieved by APCplus, which can consistently analyze injection molding process and immediately react to changes in material viscosity. These ensure high and stable product quality, significantly reduce defect.
High energy efficiency is achieved through innovative drive and temperature control systems. The Bluepower servo drive controls the pump precisely according to actual demand and energy requirement. This reduces energy consumption, production cost and carbon emissions.
The insulating sleeves in plasticizing unit promote even heat distribution and reduce heat loss. This improves process stability as well as reduces unproductive warm-up times, further enhancing productivity and energy efficiency.
5. L.K. Machinery
Brand: LKIMM
Established year: 1979 (listed in Hong Kong in 2006)
Headquarters: Hong Kong, China
Production and service network: L.K. operates production seven facilities in China, including Shenzhen, Ningbo, Kunshan, Zhongshan, Fuxin, Shanghai, and Taiwan, as well as a plant in Italy. The company has established over 60 sales offices and service centers across more than 20 countries worldwide.
Revenue (2023-2024): HKD 5.84 billion
Machine clamping force: 80-7,000 tons
Major applications: Automotive, Home Appliance, Medical, Packaging
Flagship series: FORZA (Two-platen), POTENZA (Toggle-type), ELETTRICA (All-electric)
FORZA machine offers a clamping force ranging from 4,500 to 70,000 kN, making it a compact, versatile, and efficient solution for large part production. Its flexible and modular clamping and injection matrix features plug-and-play modules. The machine delivers excellent dry cycle performance and significant energy savings. It is suitable for manufacturing car bodies, interiors, home appliances, and more.
POTENZA machine is a high-performance solution with a clamping force ranging from 800 to 10,000 kN. Equipped with a German gear pump and a permanent magnet servo motor, it offers exceptional efficiency and accuracy. The robust toggle clamp system minimizes deflection, reduces mold wear, and maximizes strength. It is suitable for manufacturing steering wheels, housewares, consumer electronics, and more.
ELETTRICA is a next-generation electric injection molding machine that incorporates European direct drive technology. It features an electric servo motor for both the ejector and metering axis, along with automatic clamping force adjustment and real-time clamping force monitoring.
LKIMM ELETTRICA series electric injection molding machine.
Hot seller: POTENZA series
Technology and product advantages: After years of development, L.K. offers a diverse range of injection molding machines, including hydraulic, hybrid, and all-electric models. The company particularly excels in large-tonnage machines, showcasing strong competitiveness in this sector.
In recent years, L.K. has introduced several innovative injection molding technologies aimed at enhancing stability and efficiency. Notably, the dual-track pumping device technology is a standout feature of the company’s large two-platen machines, designed to cater to the demands of ultra-large cages, pallet boxes, inspection wells, and other environmentally friendly plastic products.
Furthermore, the next generation of direct-clamp technology has been implemented in the LENA LA300 injection molding machine. The non-contact design between the Corinthian column and the plate minimizes wear on the hinges while preventing potential damage to the plates and molds, thereby increasing the machine's durability.
L.K.'s multi-component injection molding machines can be equipped with a large turntable featuring 2-3 stations, making them ideal for producing multi-color and multi-material products such as automotive lights, home appliances, and everyday essentials. The specialized plate, designed to work with the central rotor, supports the large turntable and ensures stable, high-quality injection molding.
Additionally, L.K. incorporates an ultra-large direct-drive electric melt servo system in some of its large injection molding machines. This technology synchronizes ejection, melting, and mold opening, effectively meeting the production demands of complex processes and enhancing overall production efficiency.
Read more: Comparison: 10 renowned Chinese injection molding machine brands (Part 2)

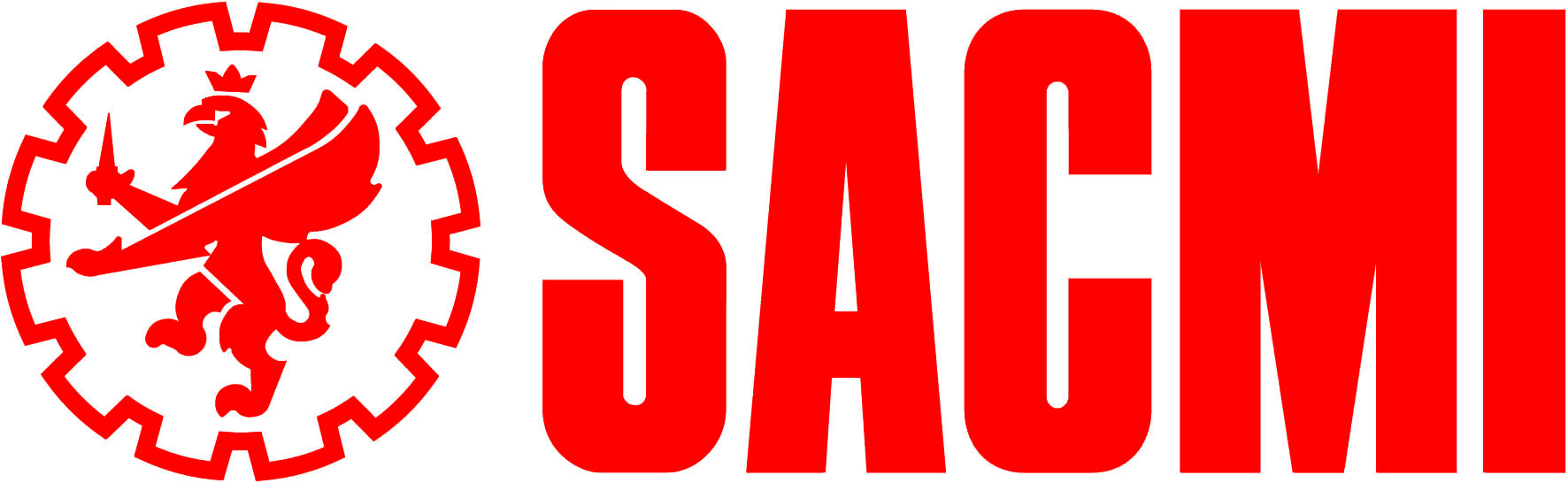

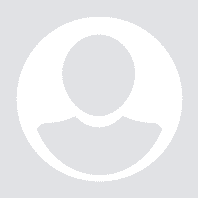

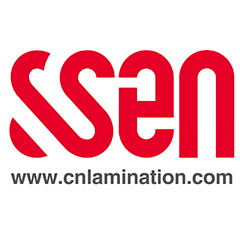

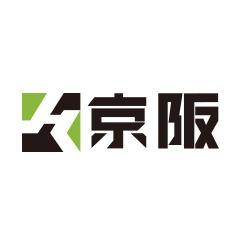

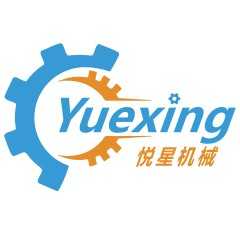

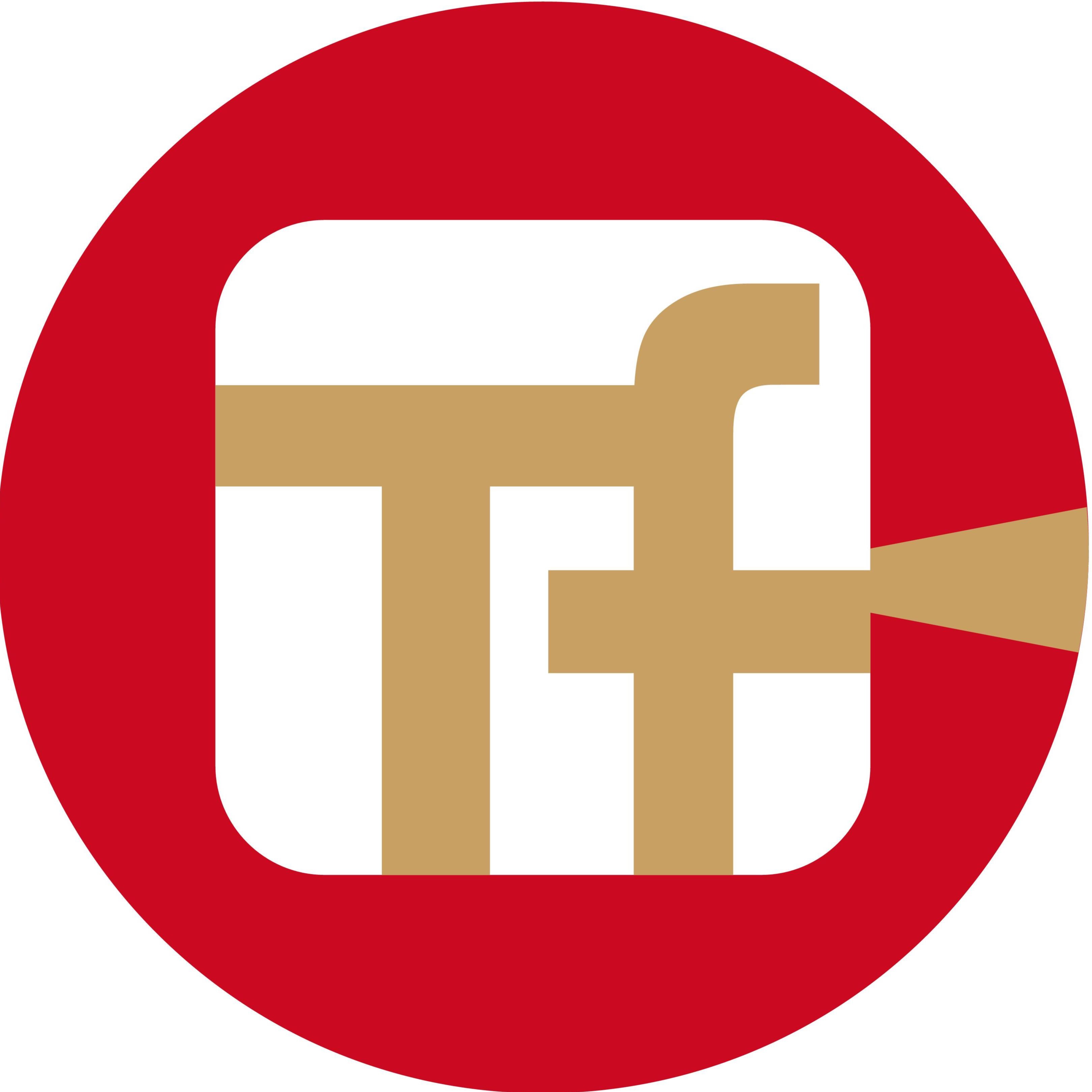

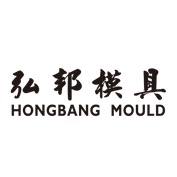

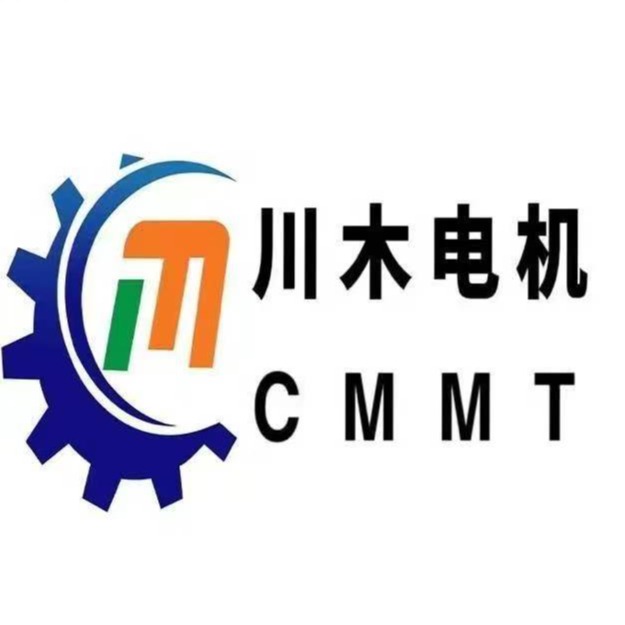

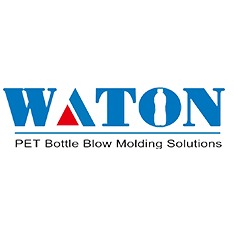

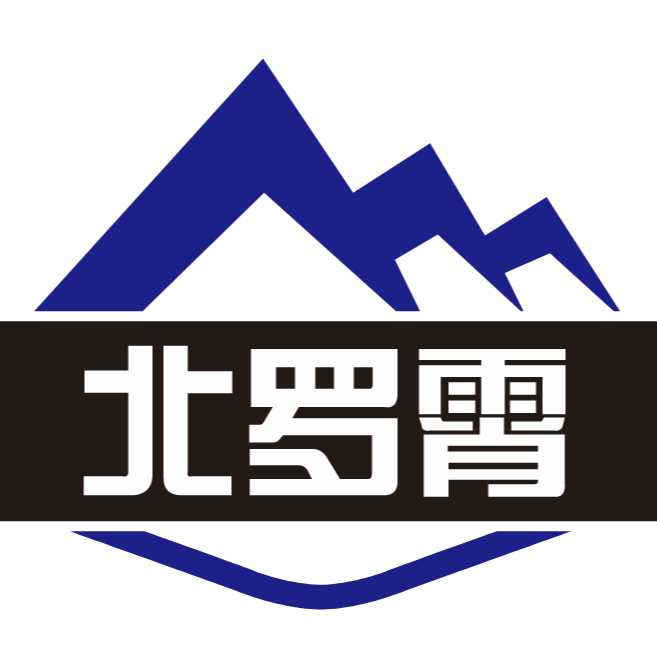

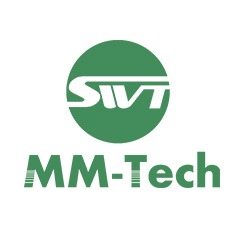

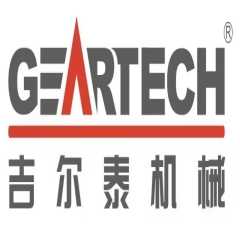

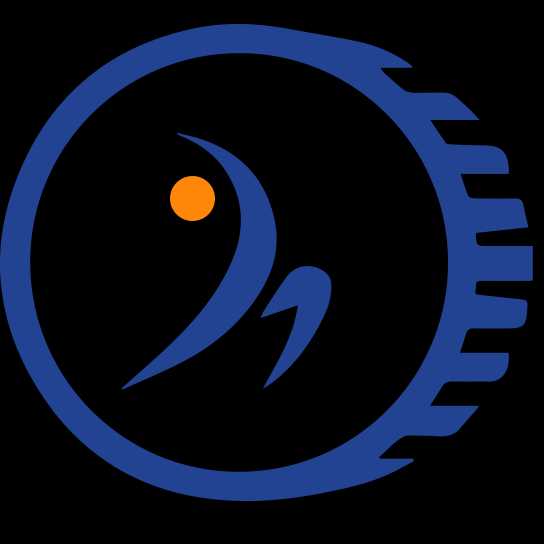

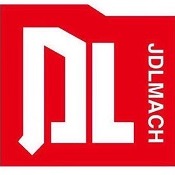

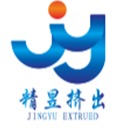

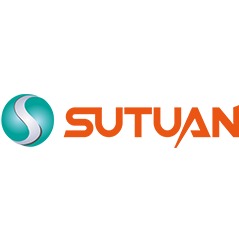

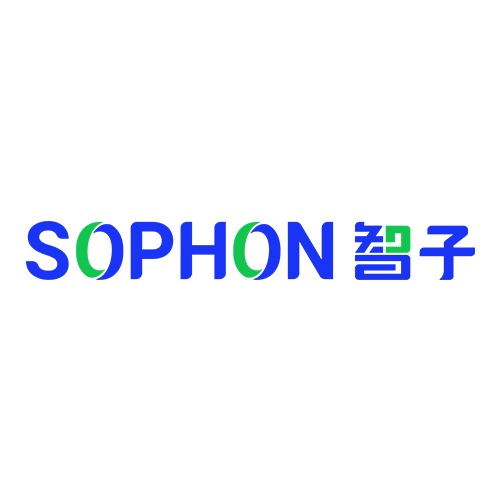

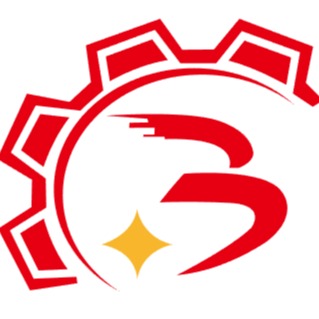

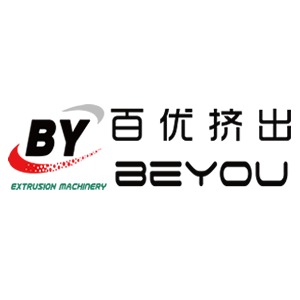

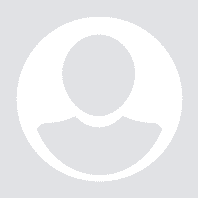

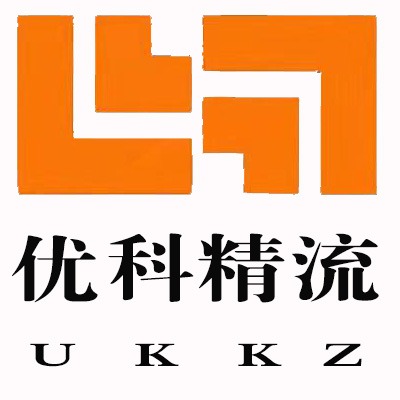

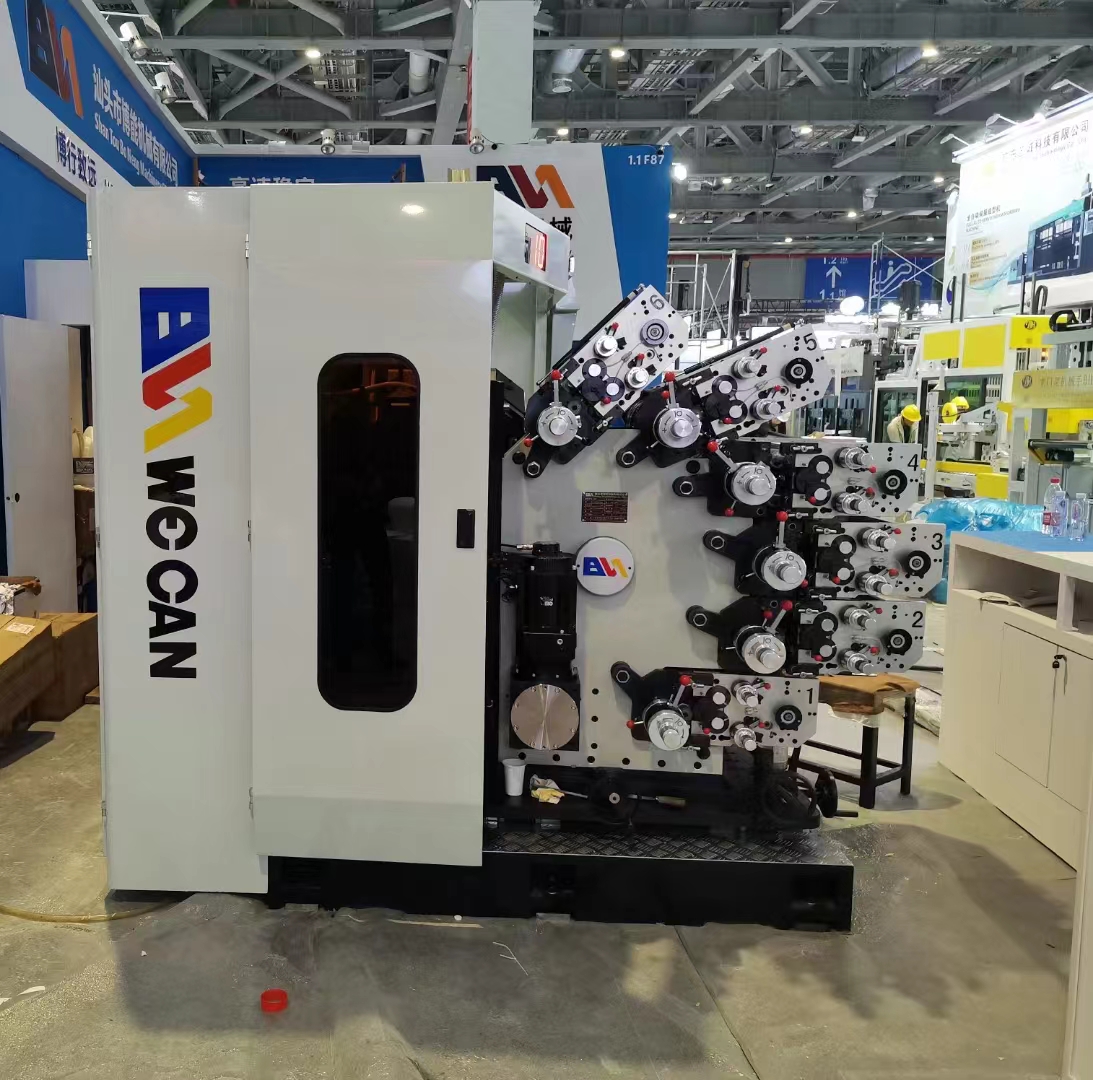

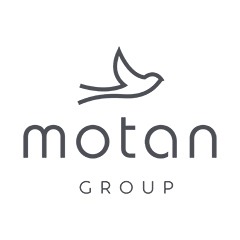

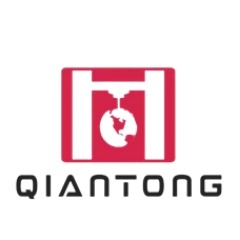

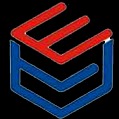

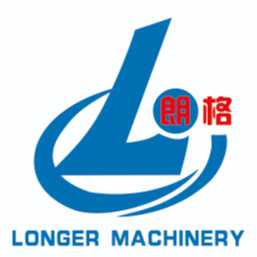

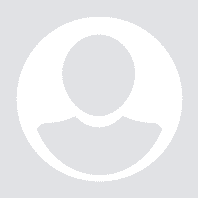

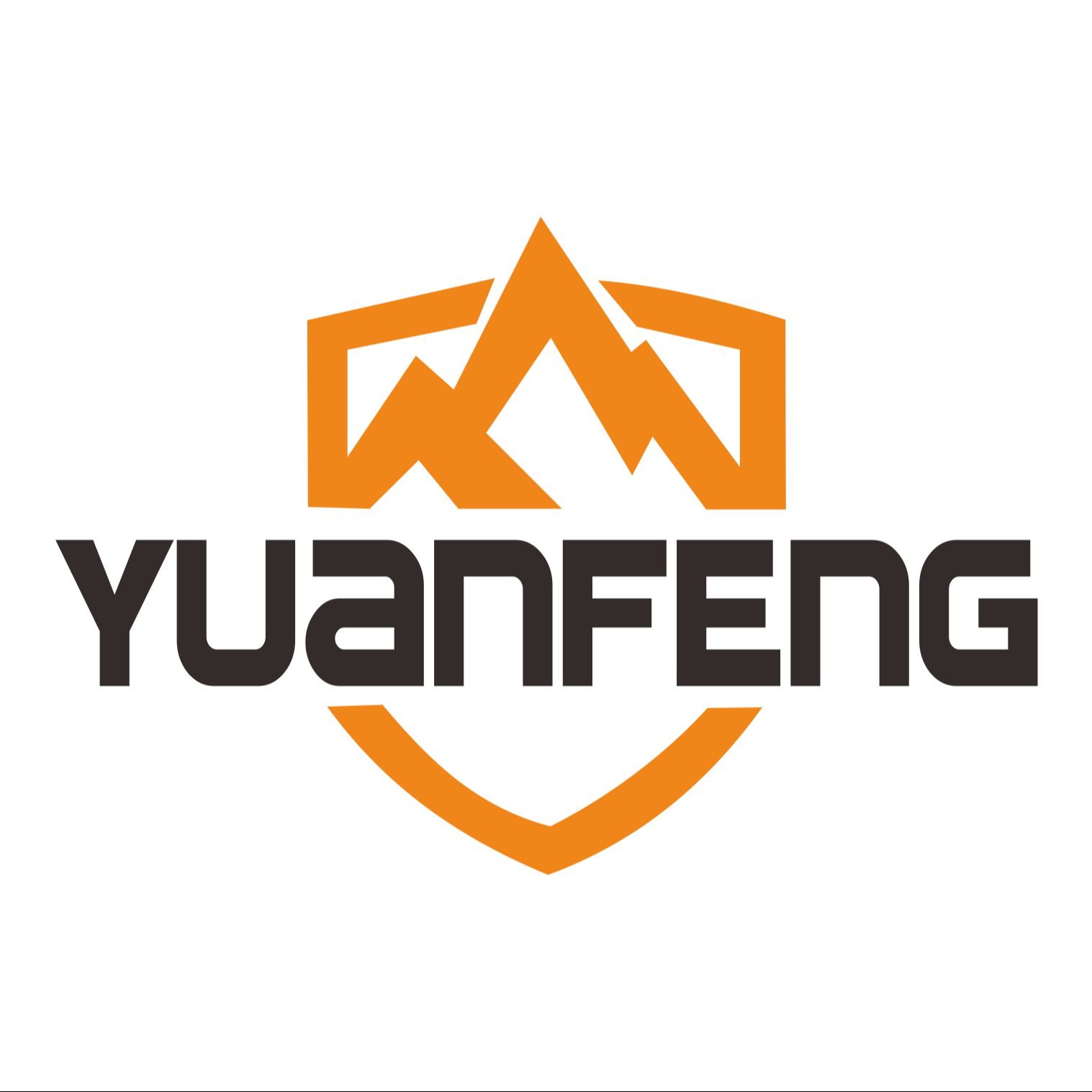

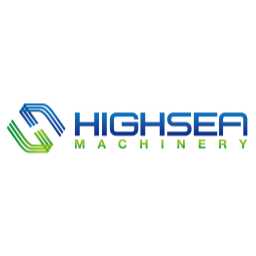

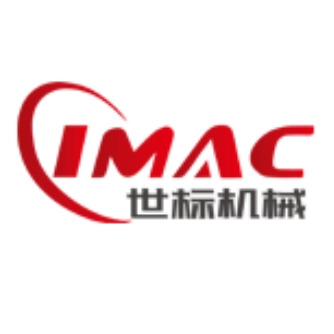

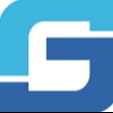

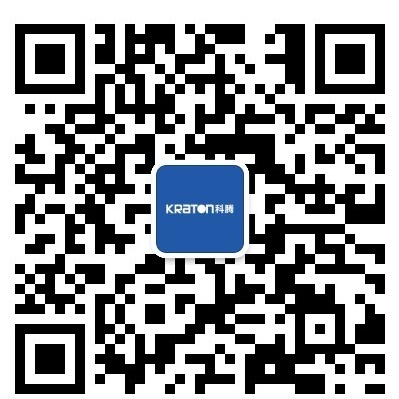

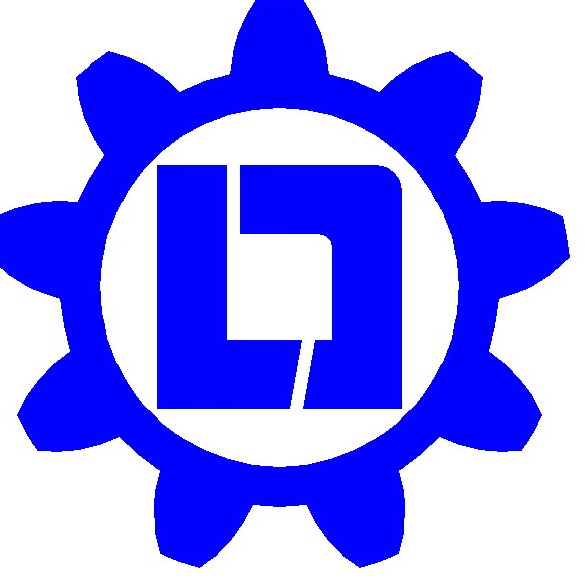

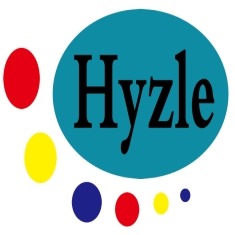

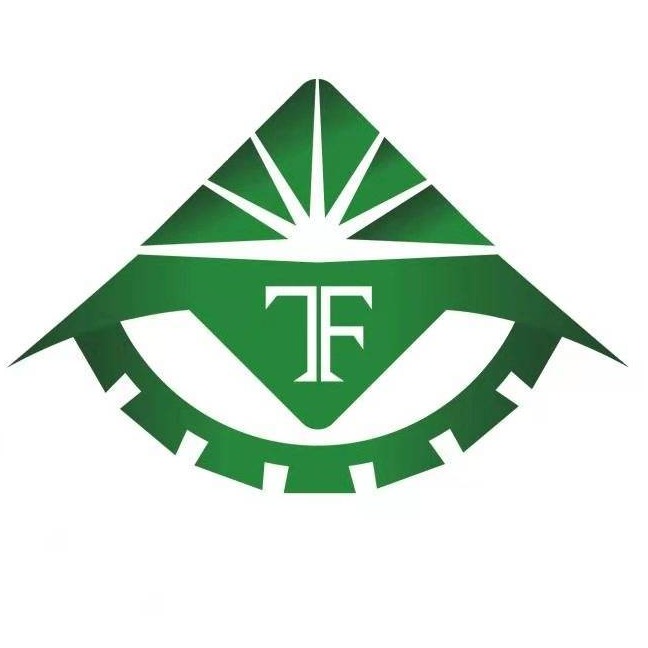

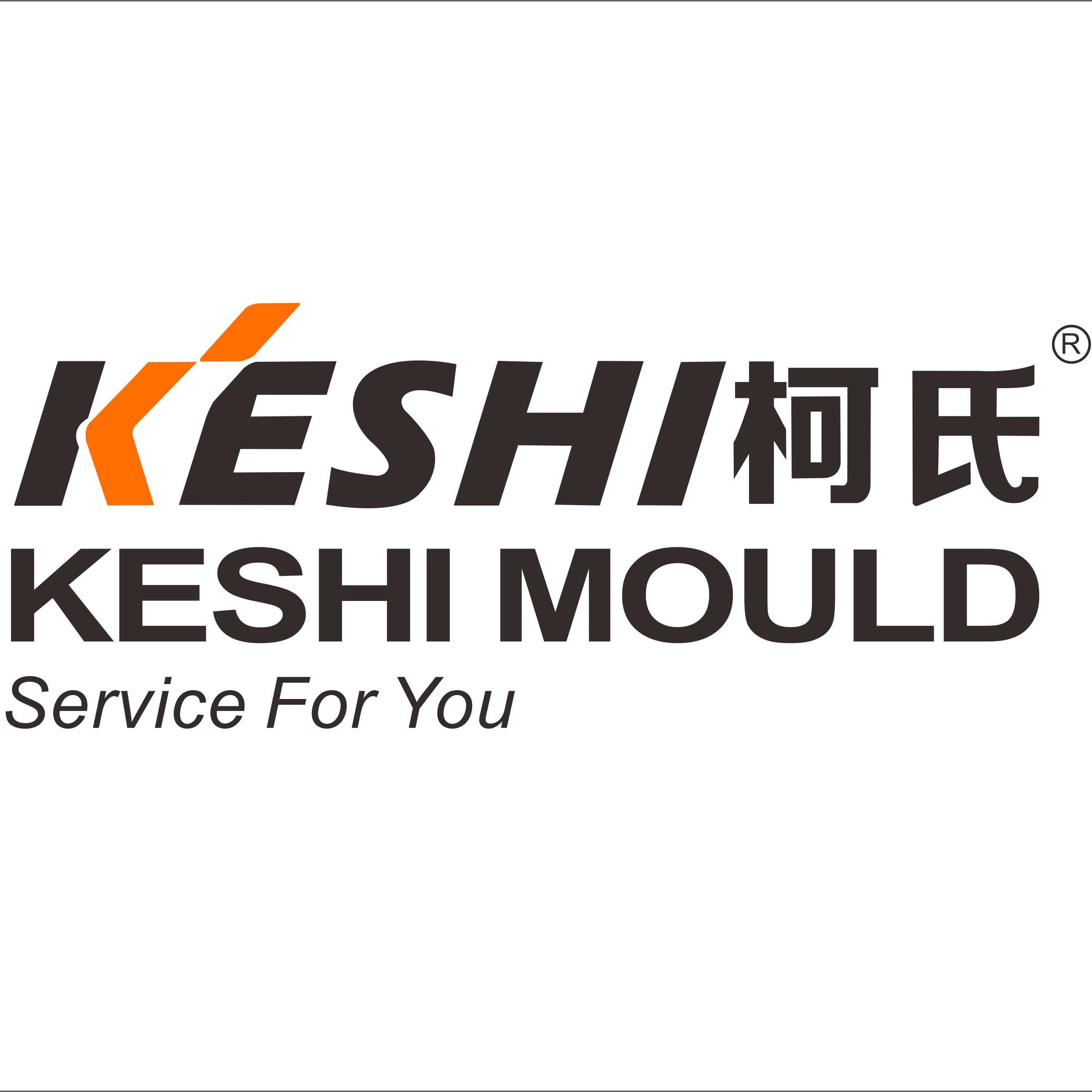

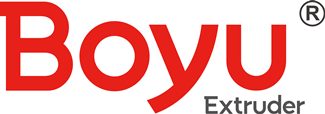

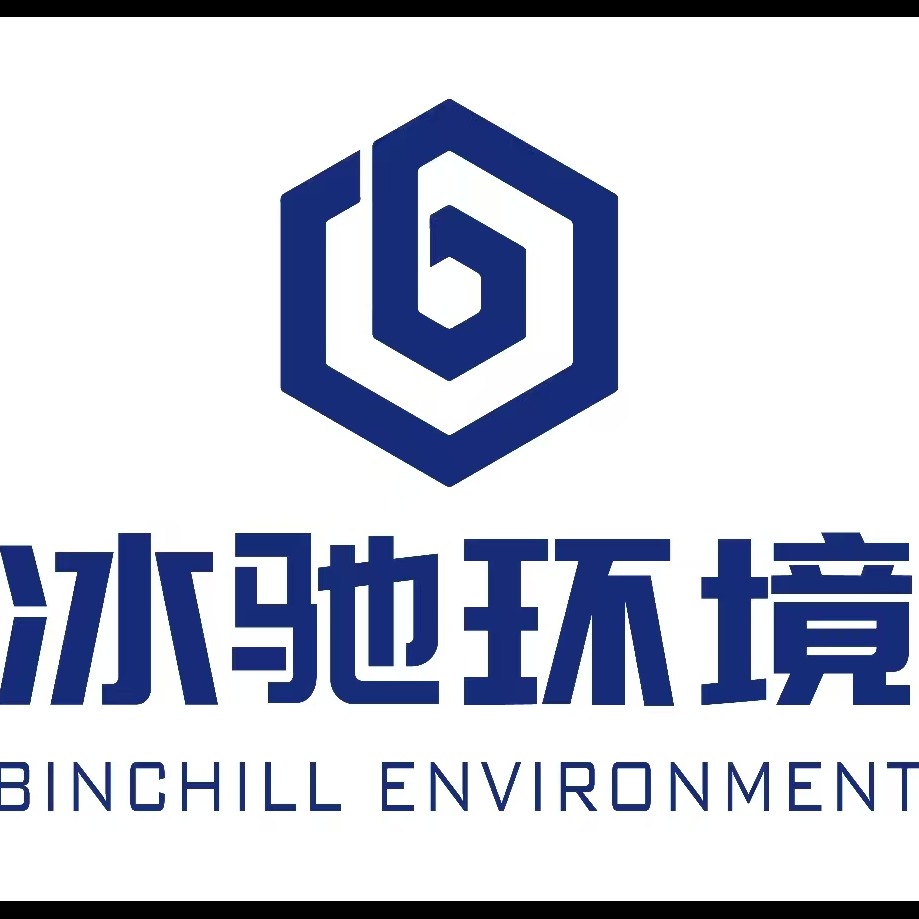

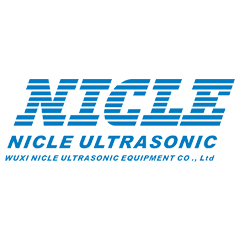

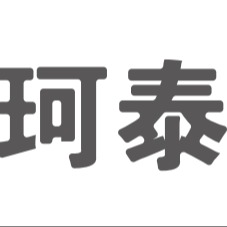

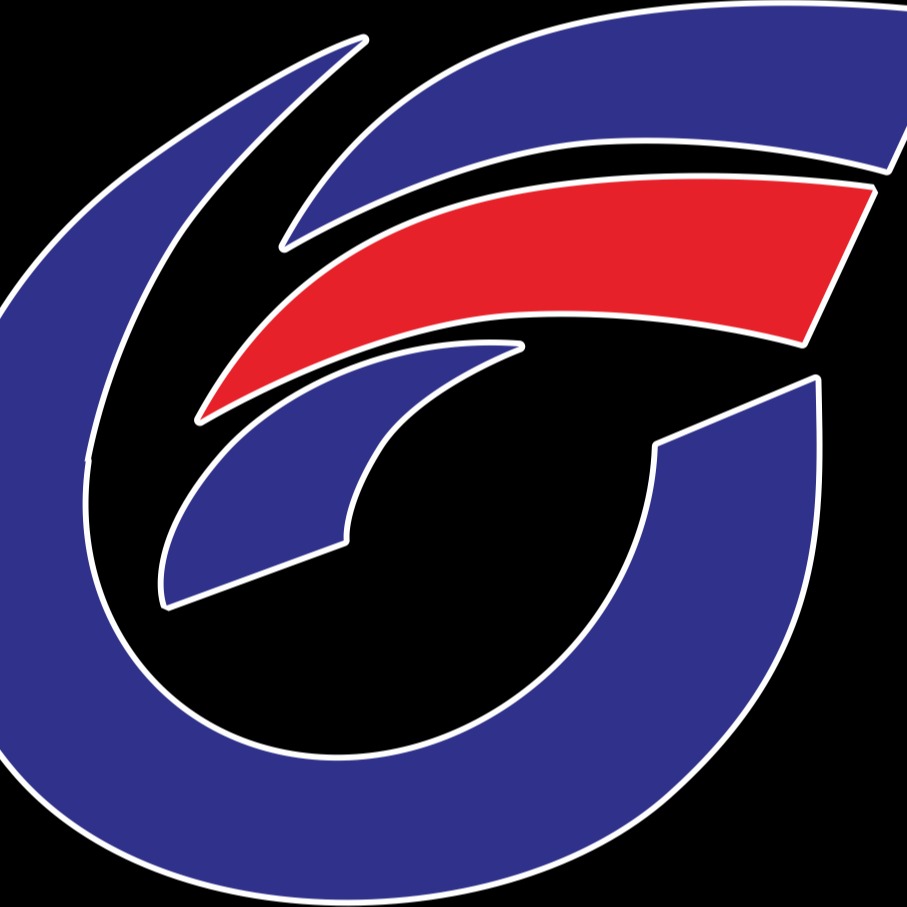

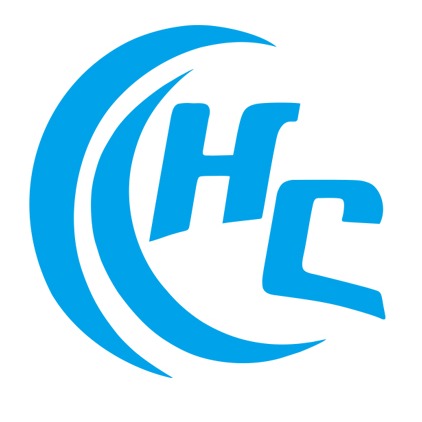

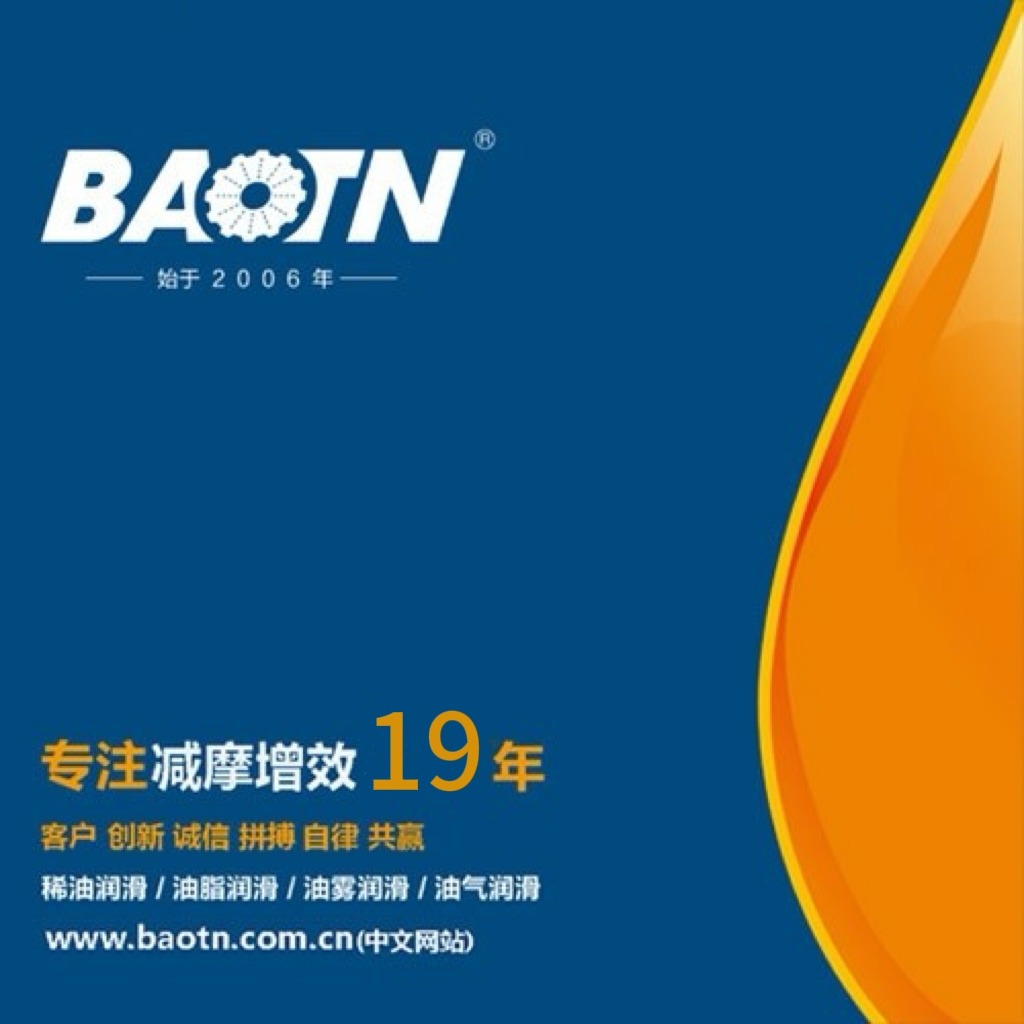



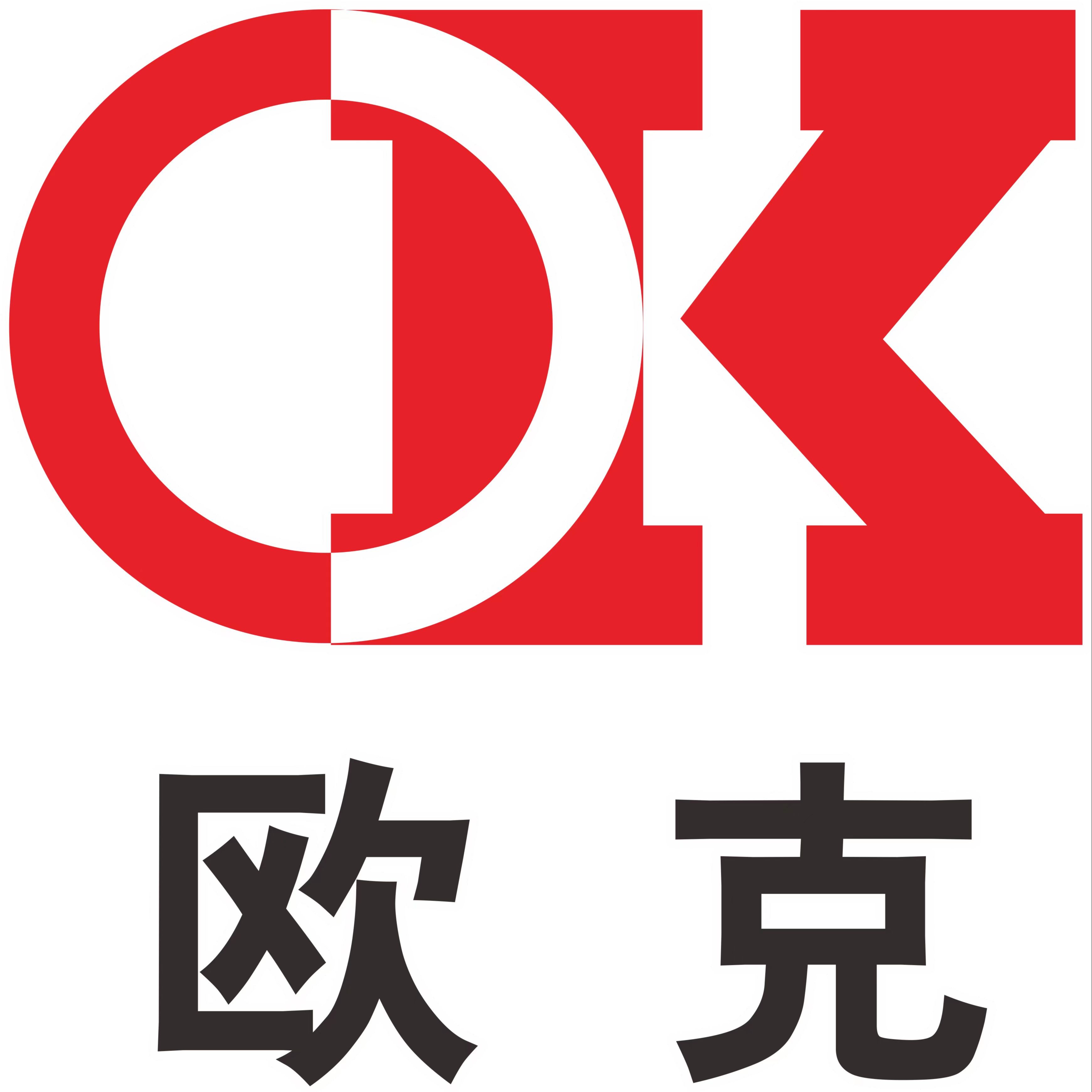

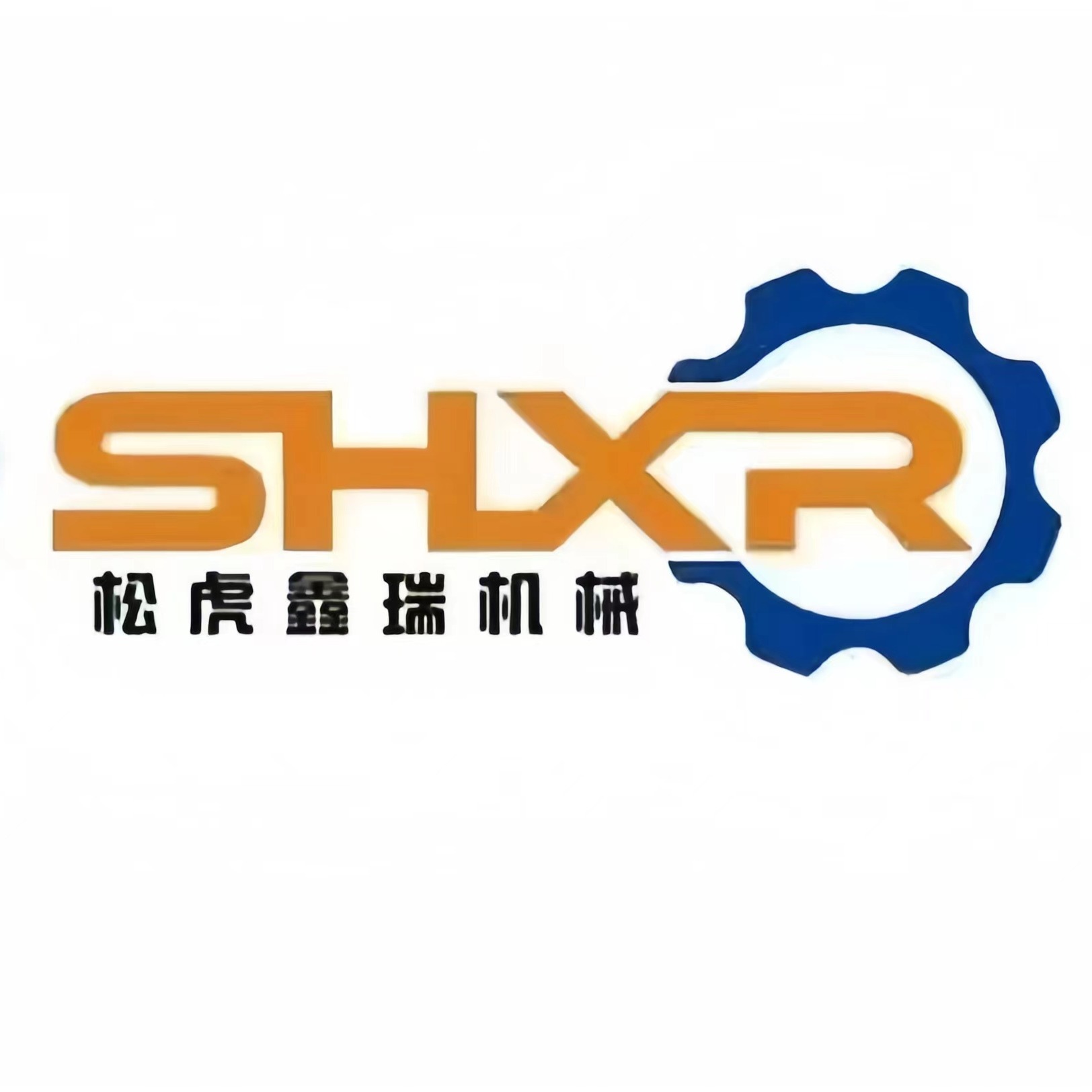

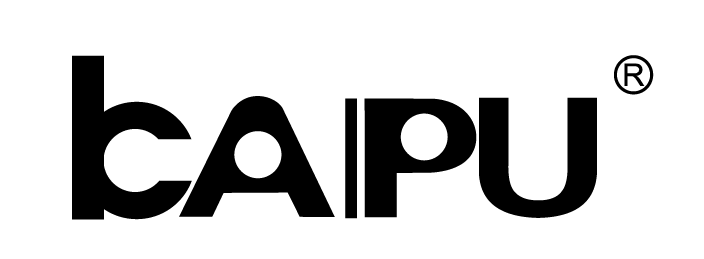

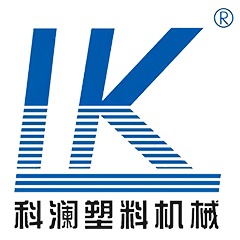

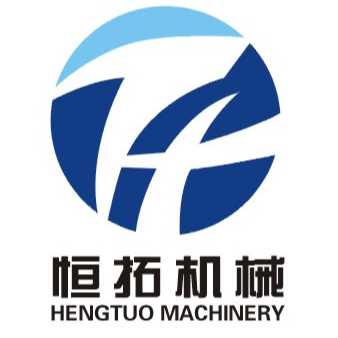

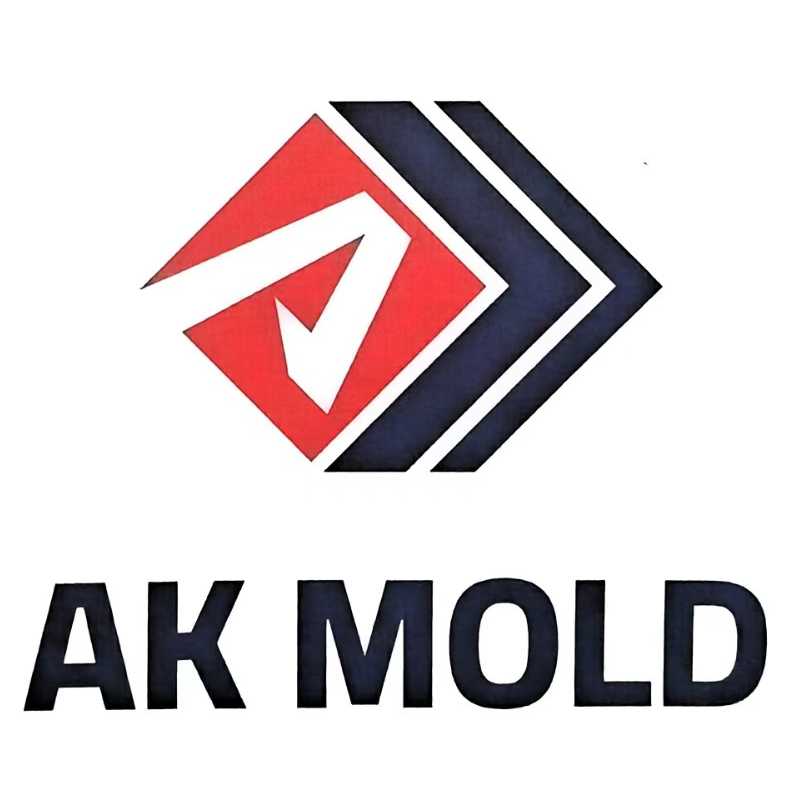

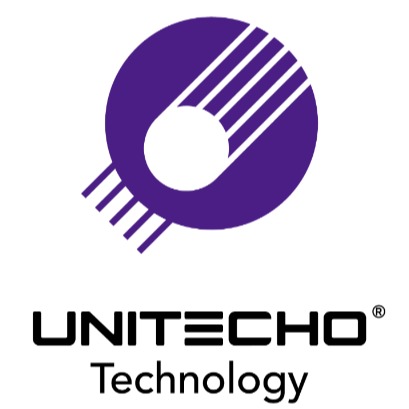

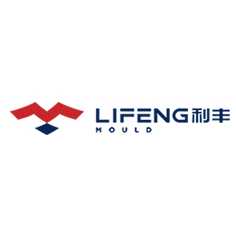

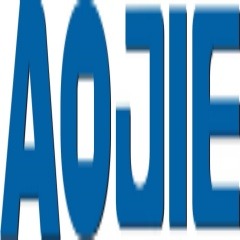

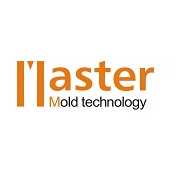

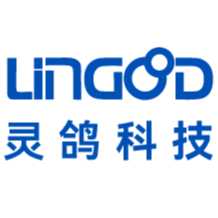

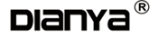

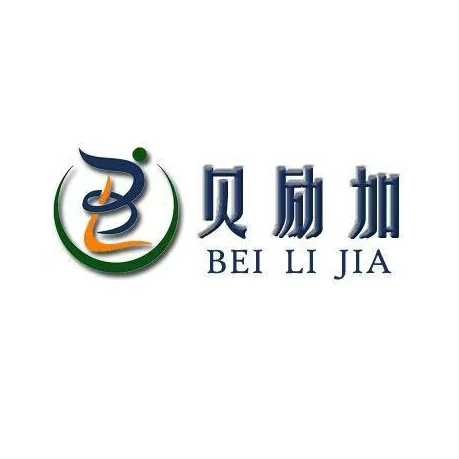

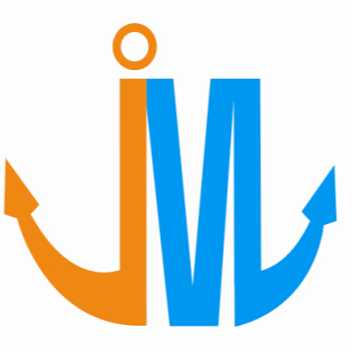

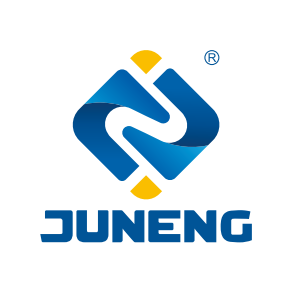

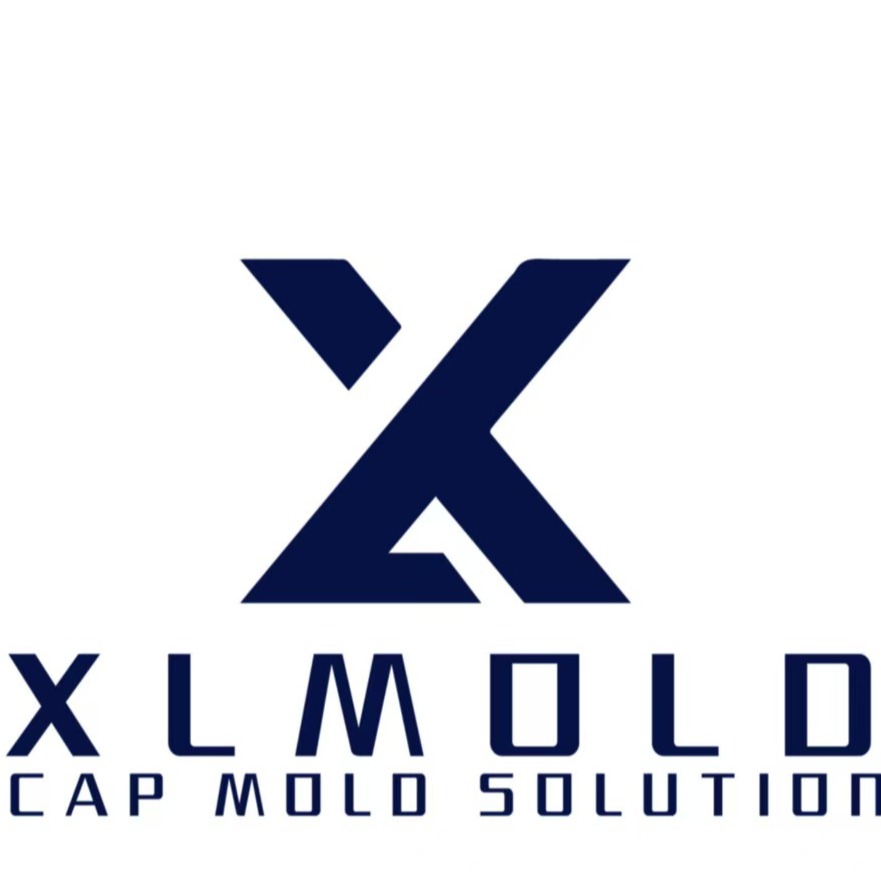

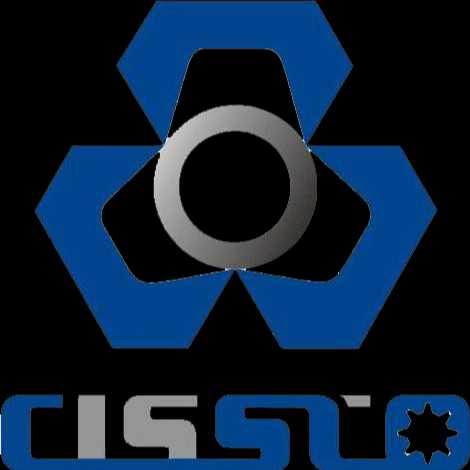

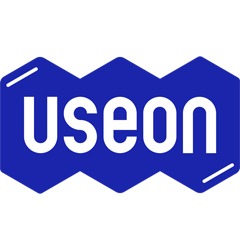

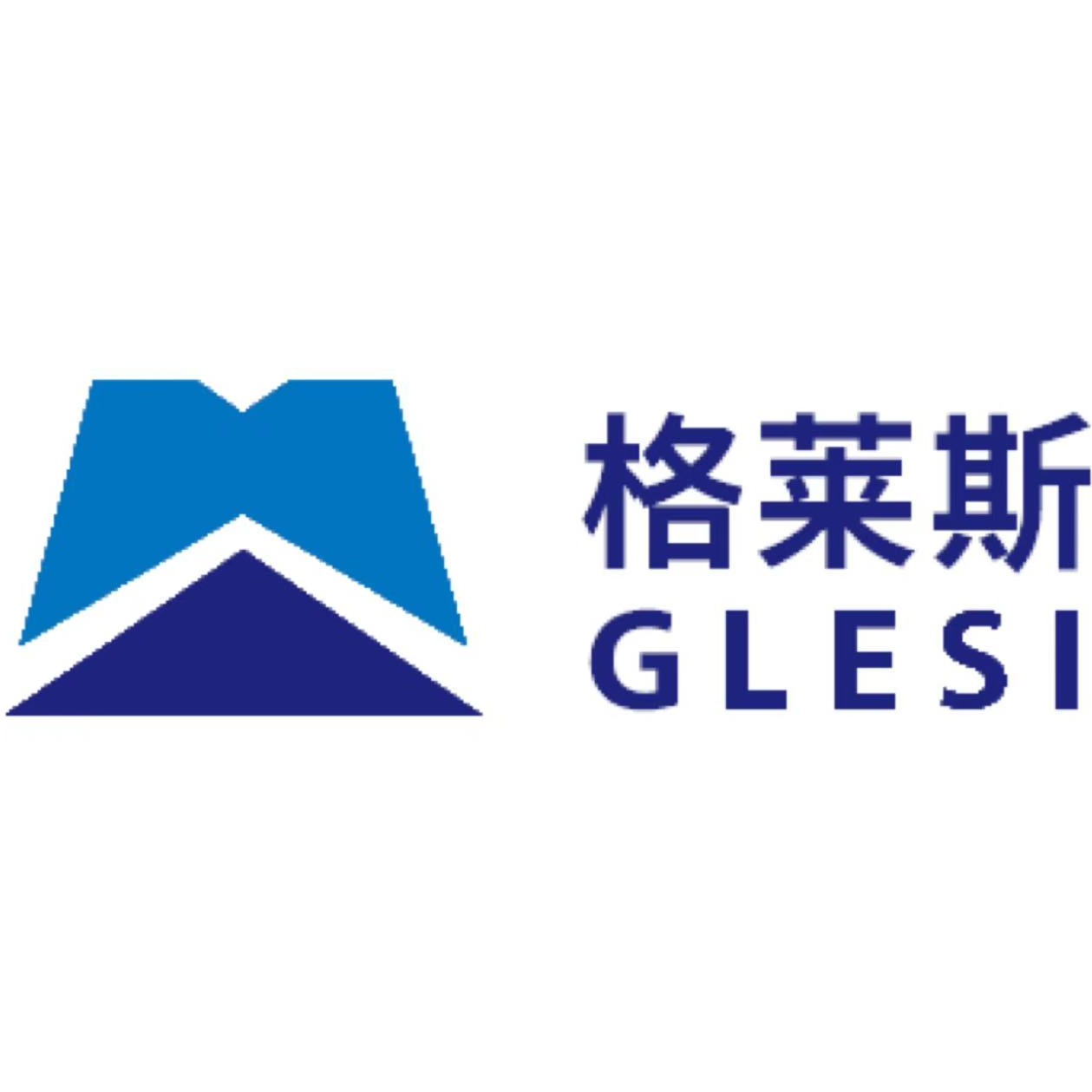

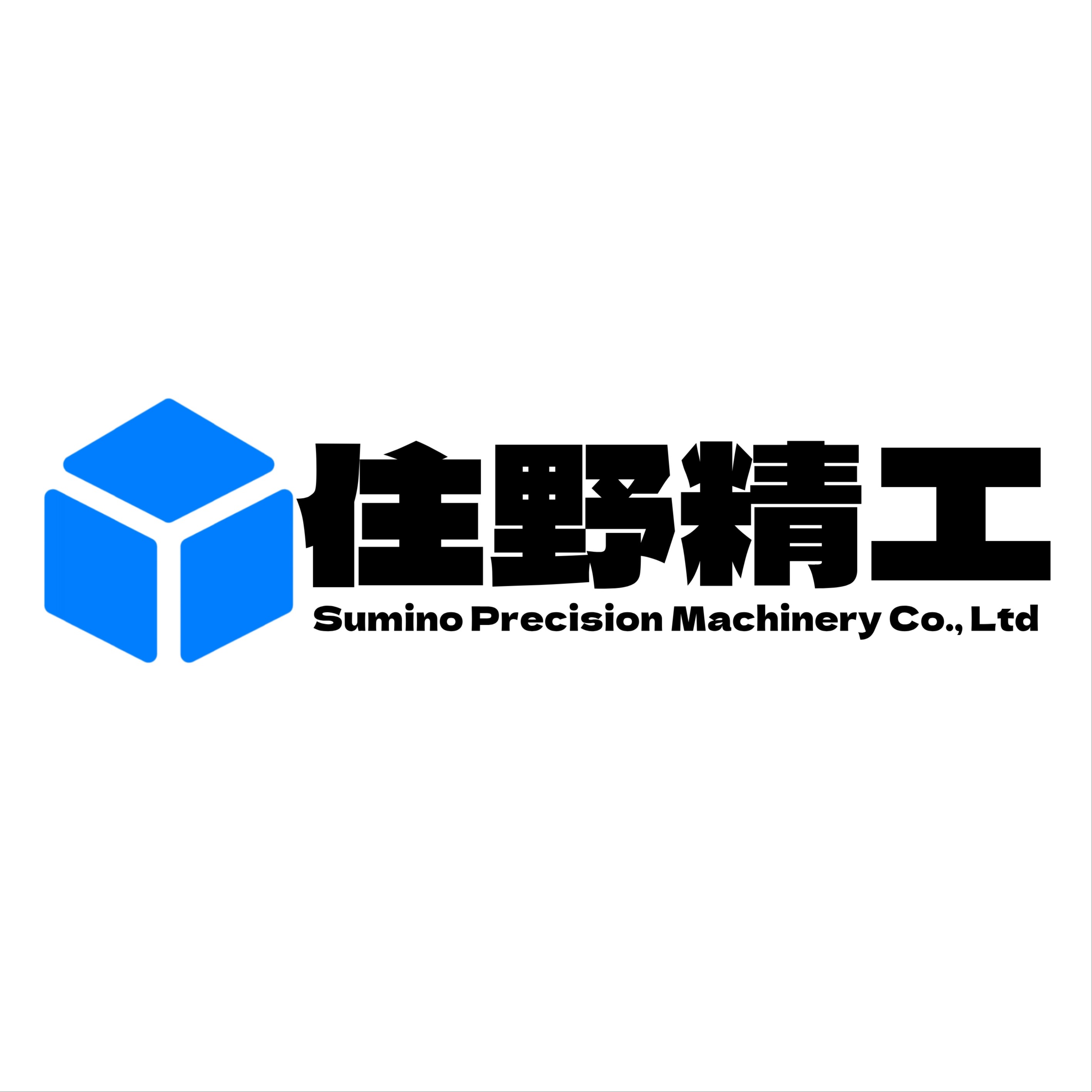

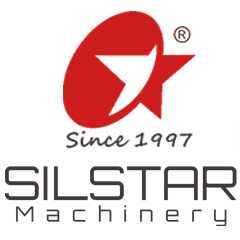

Recommended Articles
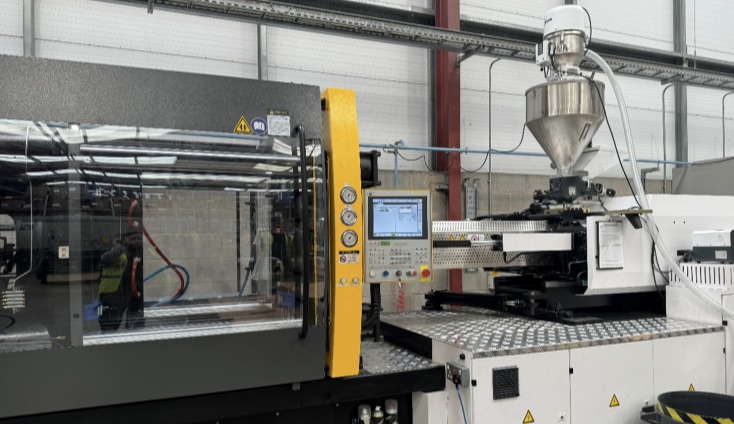

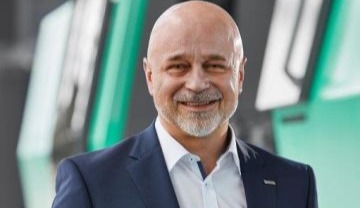

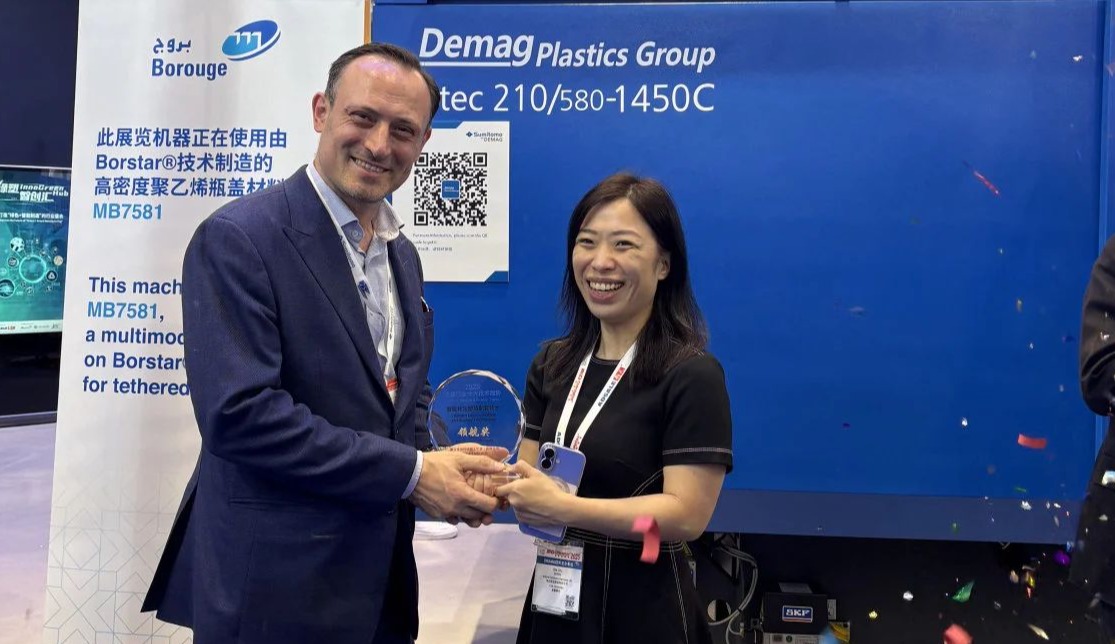

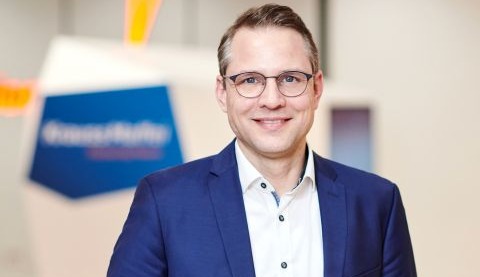

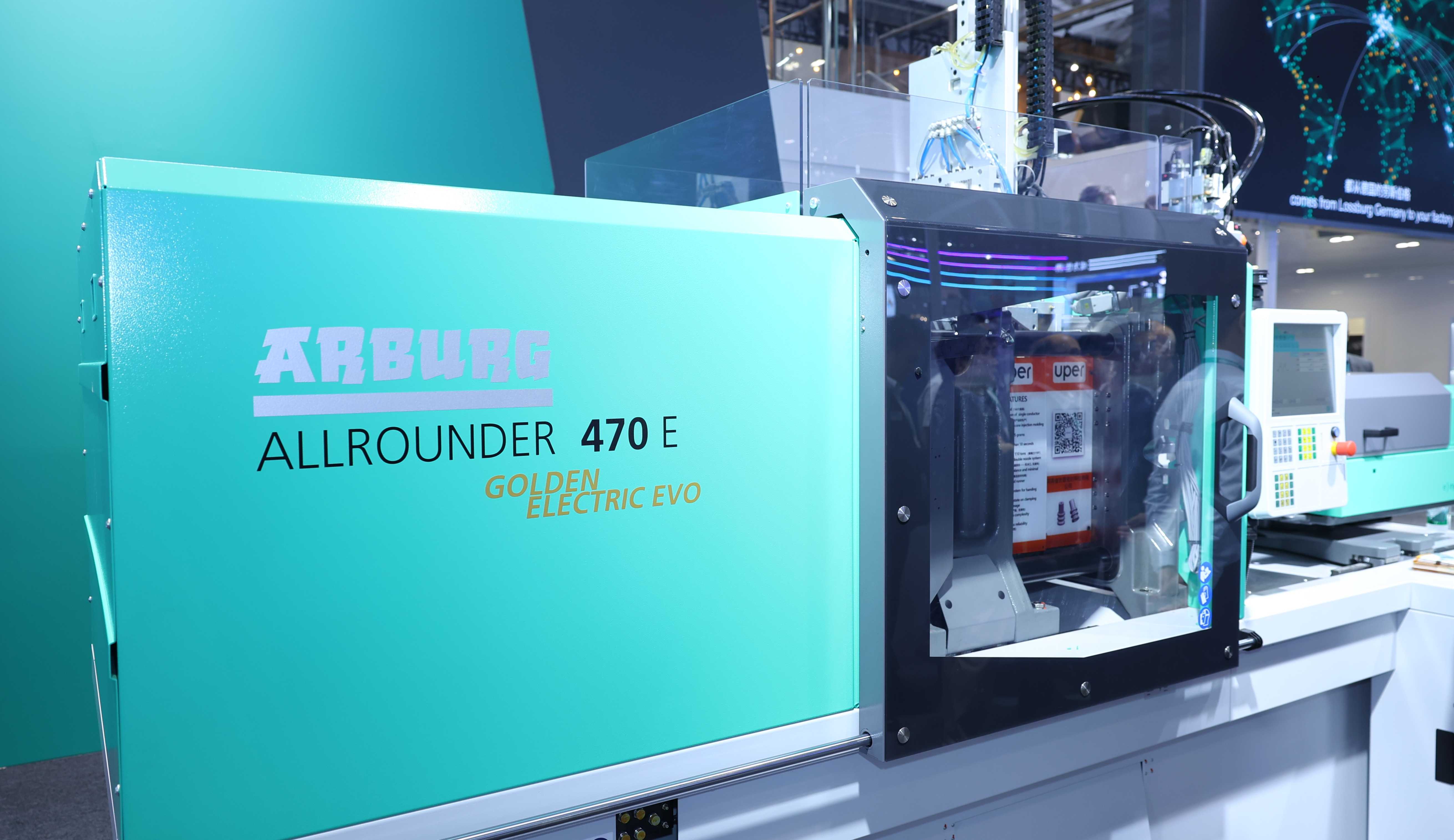

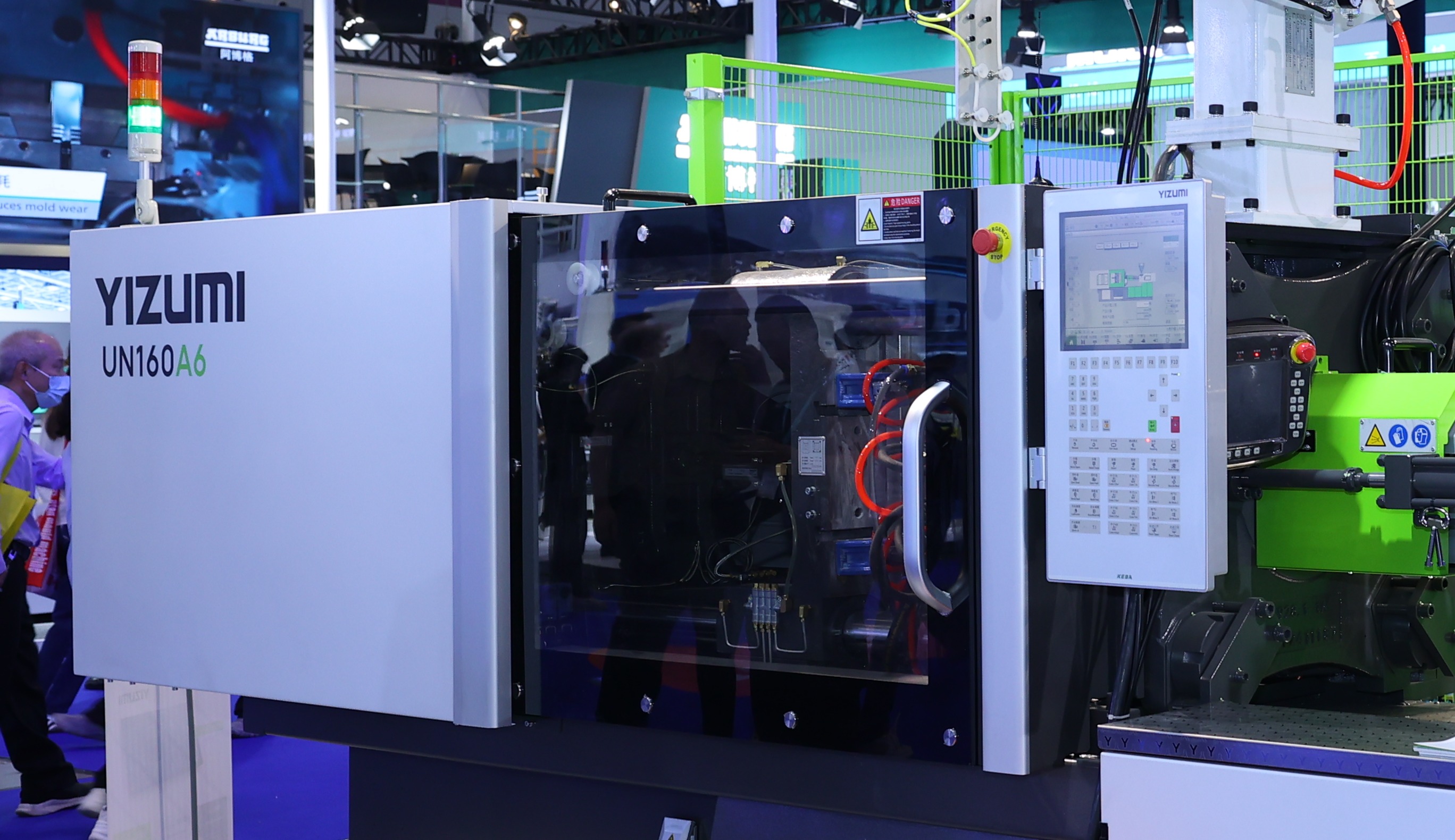

Must See






- Hot Specials
You May Be Interested In

Change
- People
- Company
Hot Tags