- Comment
(0)
Home > News > Mold/Hot Runner
Mold-Masters debuts Sprint APEX technology for caps applications
As one of the largest hot runner/controller technology supplier, Mold-Masters showcases its Sprint APEX technology in packaging industry and upgraded mounting system Fusion G3 at CHINAPLAS 2024.
David Yang, President of Mold-Masters Asia, introduces that these two technologies make their debut in Asia Pacific. Sprint APEX acts as an environmental stress crack resistance (ESCR) solution while Fusion G3 is an upgrade of Fusion G2. These fulfil customers' changeable demands and offer more economical and durable solutions.
David Yang, President, Mold-Masters Asia.
For caps and closures production, achieving and maintaining a proper ESCR level is a Key Performance Indicator (KPI) for molding equipment. The Sprint APEX gate seal is designed to significantly minimize the presence of injection flow lines, which can increase the ESCR level of CSD caps by up to 40%, as determined and validated through third-party testing at Dow Pack Studios. In addition, compared to standard gate seal, Sprint APEX gate seal improves color-change performance by up to 65%.
Fusion G3 is a pre-assembled and pre-wired system which allows quick and easy one-step drop-in installation and connection. It reduces up to 70% time to assemble and install, ensuring the mold back into production as quickly as possible. The system utilizes third generation nozzle, a threaded nozzle base available for enhanced leak protection. Extended nozzle length and multiple heater zones enhance thermal control, achieving precise thermal profile.
Fusion G3 system focuses on high quality economical production of medium to large parts. It fits for automotive, appliance, logistic and many other similar applications.
"In 2023, Mold-Masters achieved steady sales growth in electronics industry while orders of co-injection molding technology in medical sector increased 50%," says Yang. Moreover, the company also provided solutions to almost 5,000 projects related to new energy vehicle in China, including battery, headlight and connector.
Mold-Masters' industry-leading co-injection multi-layer systems are available for injecting light blocking barrier materials as the core layer for thin wall packaging applications. Light blocking barriers reduce light transmittance by up to 99.9% to extend product shelf life and preserve freshness and flavor of dairy products.
The company offers co-injection hot halves for thin wall packaging in any cavitation. The light barrier is compatible with both virgin and recycled material. Dosing of Black Core can be customized to meet the specific requirements of the molded part.
Debuted in Asia Pacific, Sprint APEX significantly minimizes the presence of injection flow lines.
Yang adds that Mold-Masters and DME, as both under Hillenbrand, further collaborate. By leveraging DME's expertise in standard parts, Mold-Masters strives for more breakthroughs in mold production. At the same time, Mold-Masters is launching the Eco One hot runner system for mid- to low-end market, bringing cost effective technology and service to customers.
Construction and operation of Mold-Masters' fourth automated production line is in progress according to plan. Mold-Masters China started its development plan on intelligent factory eight years ago. So far the company operates with factory management system based on Distributed Numerical Control (DNC), AI system on Material Resource Planning (MRP), production with Advanced Planning Systems (APS), as well as three automated production lines.
"With more and more products manufactured with DNC management system and automated production line, Mold-Masters can achieve more stable product quality and shorter delivery time," emphasizes Yang.
Booth: 5.2F15

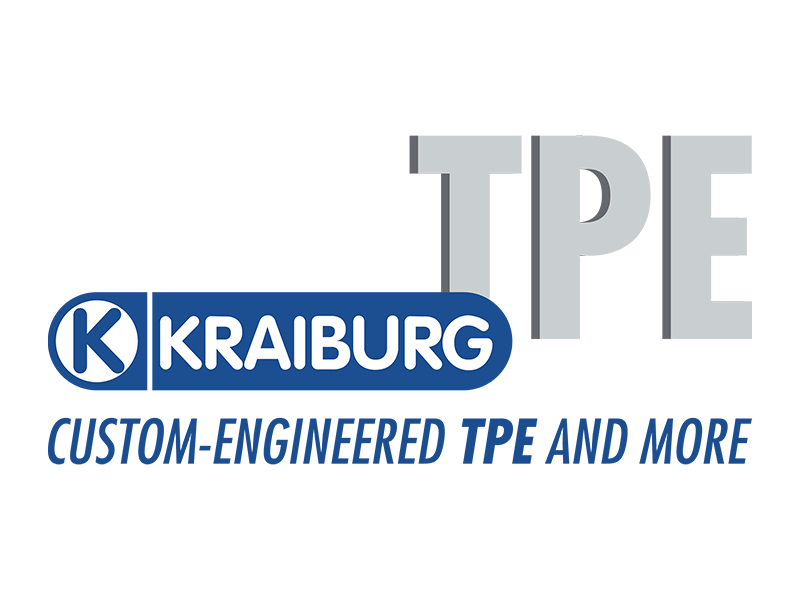

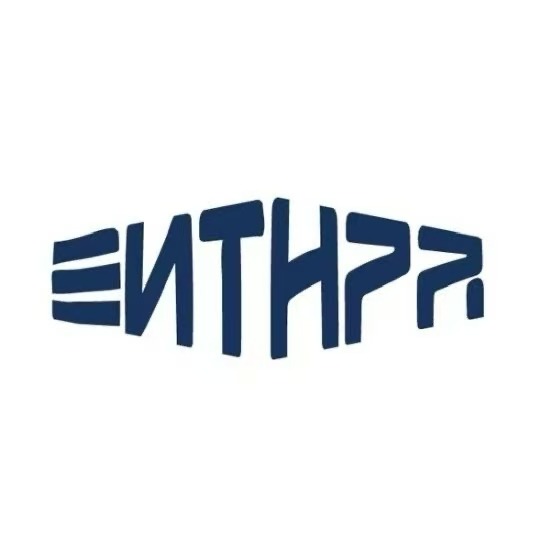

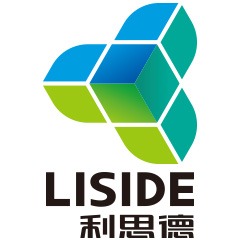

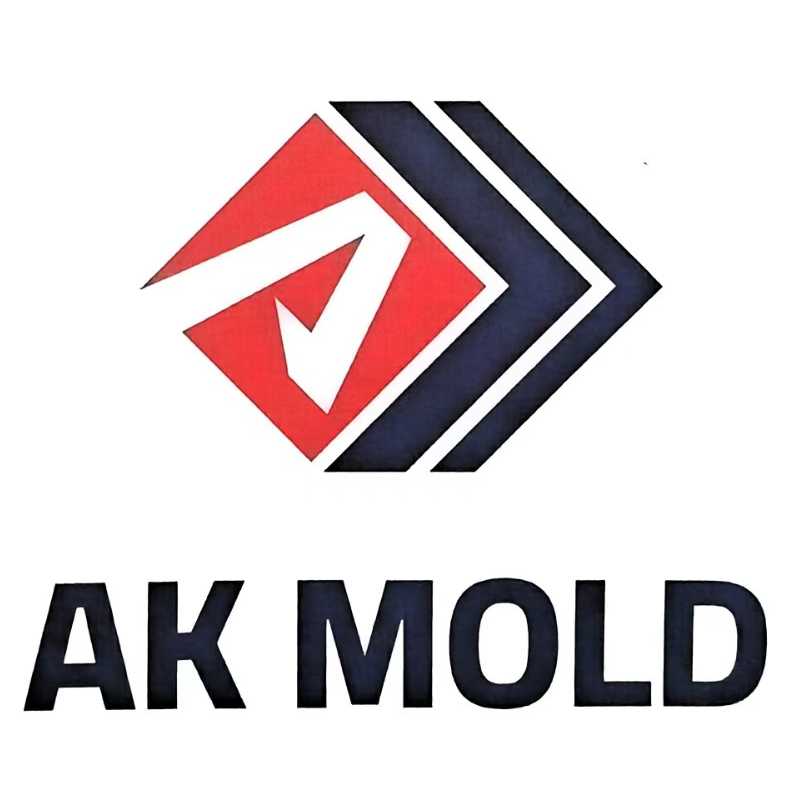

Leave Comment
All Comments
Recommended Articles
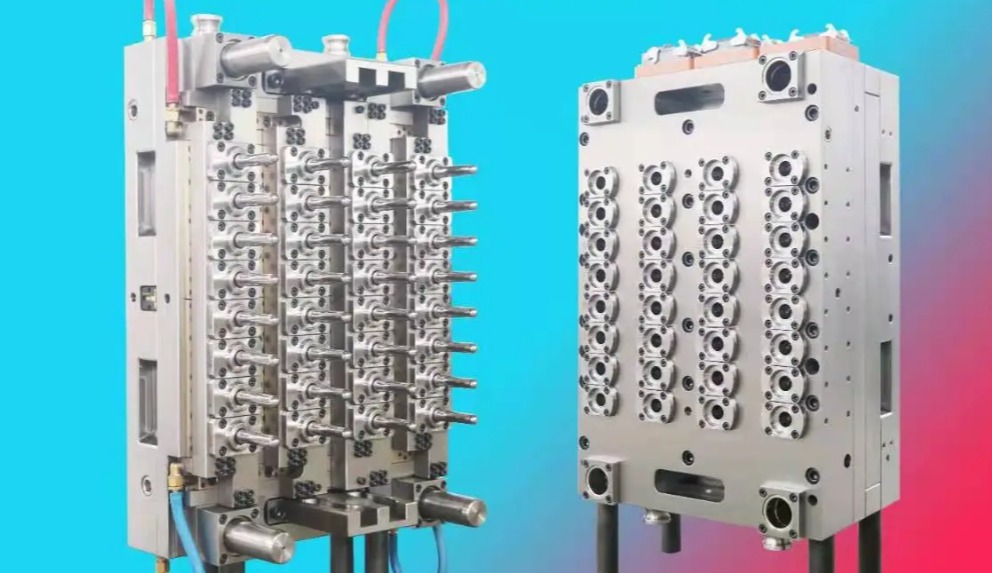

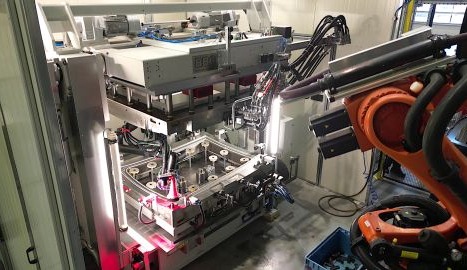

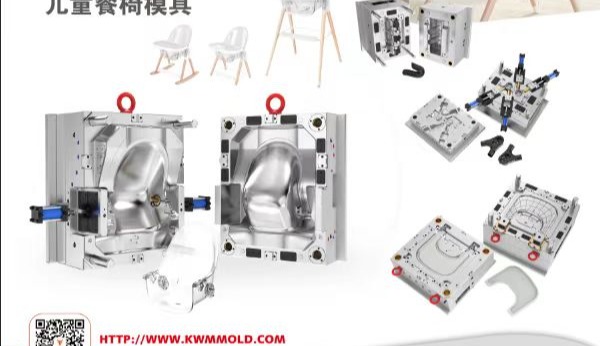


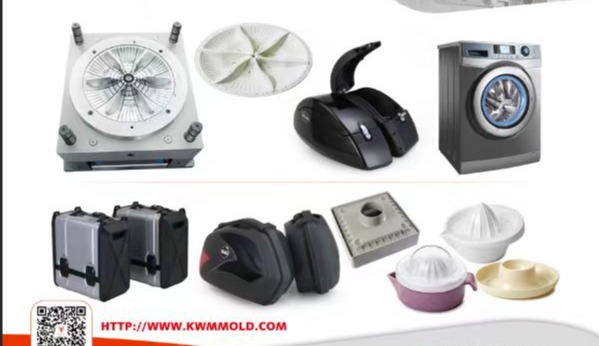


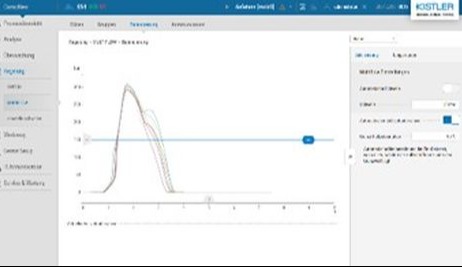

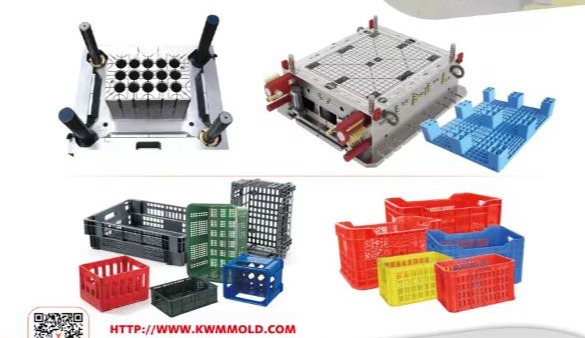


You May Also Like

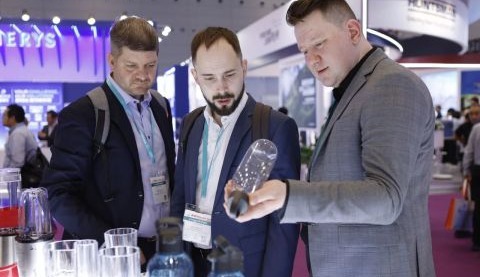
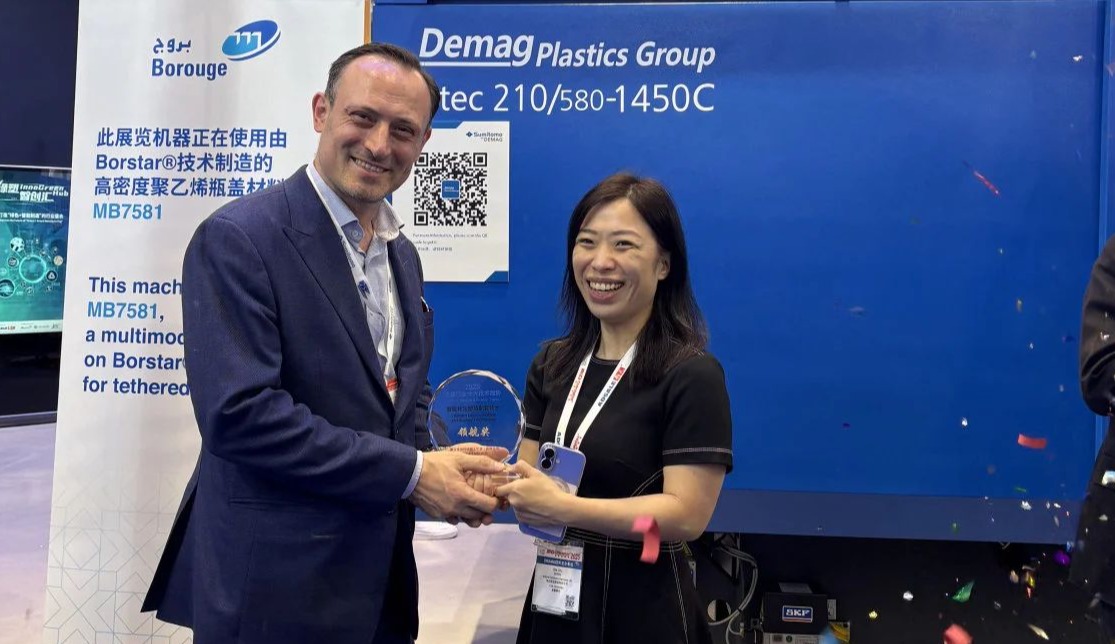
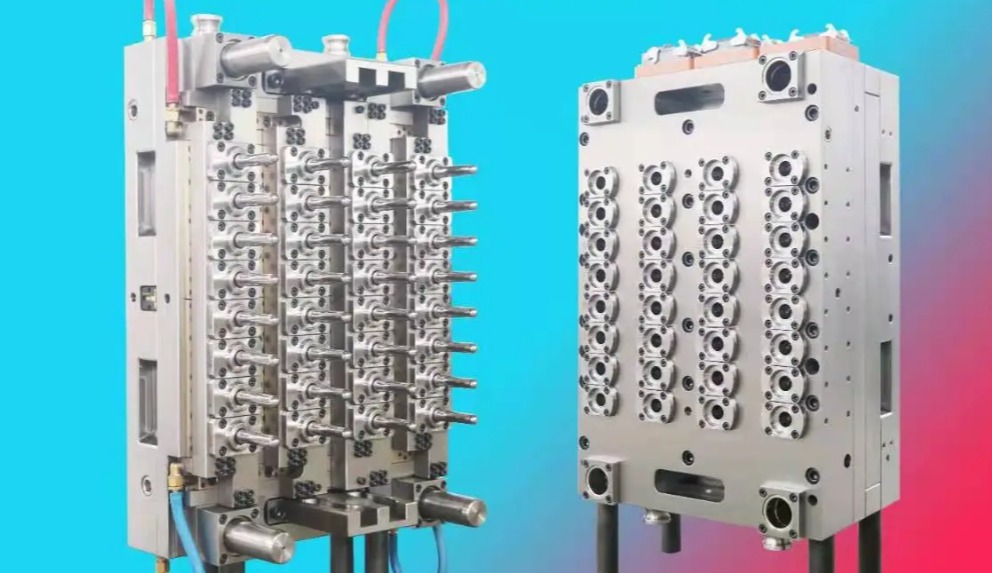
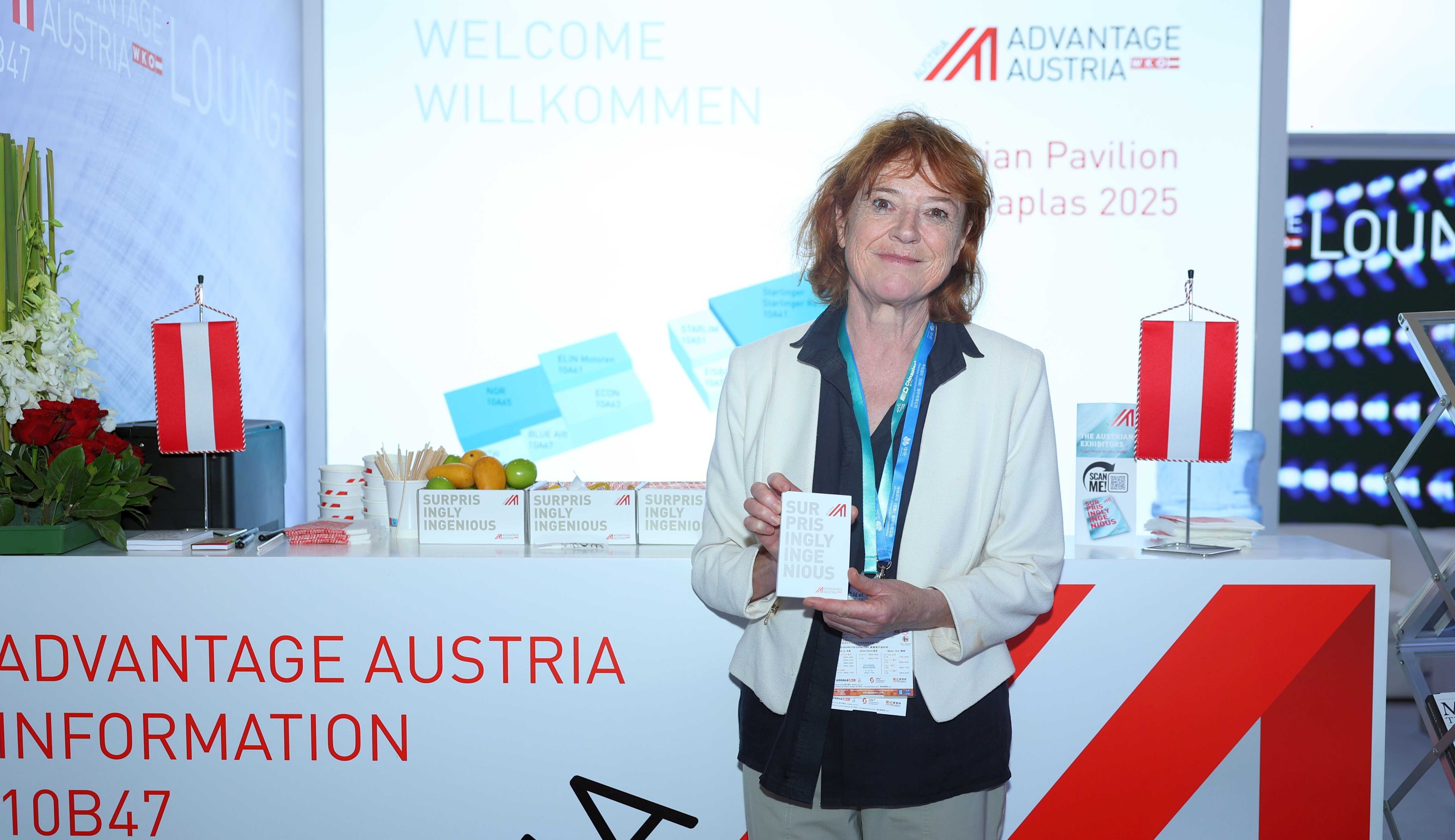
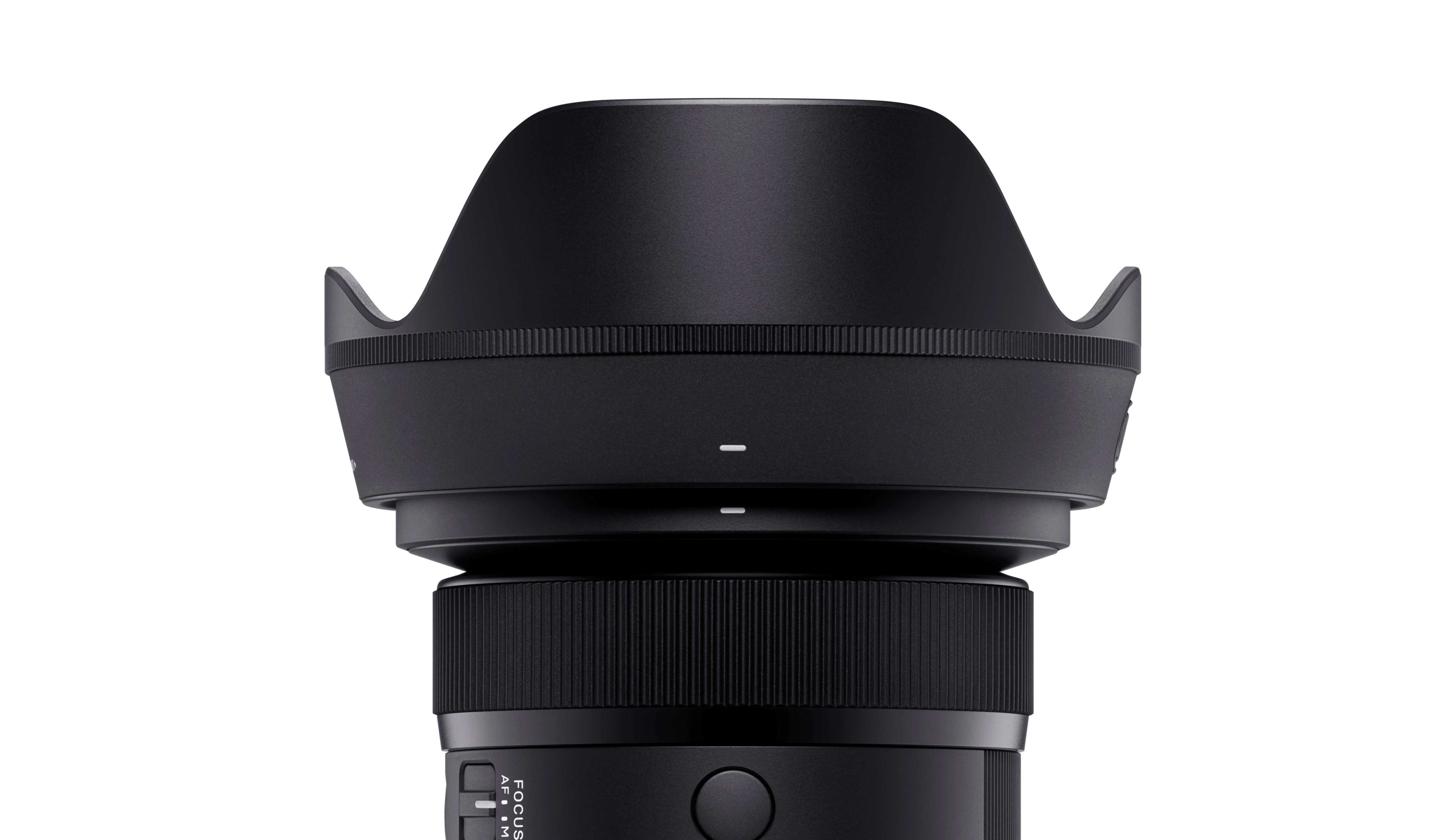
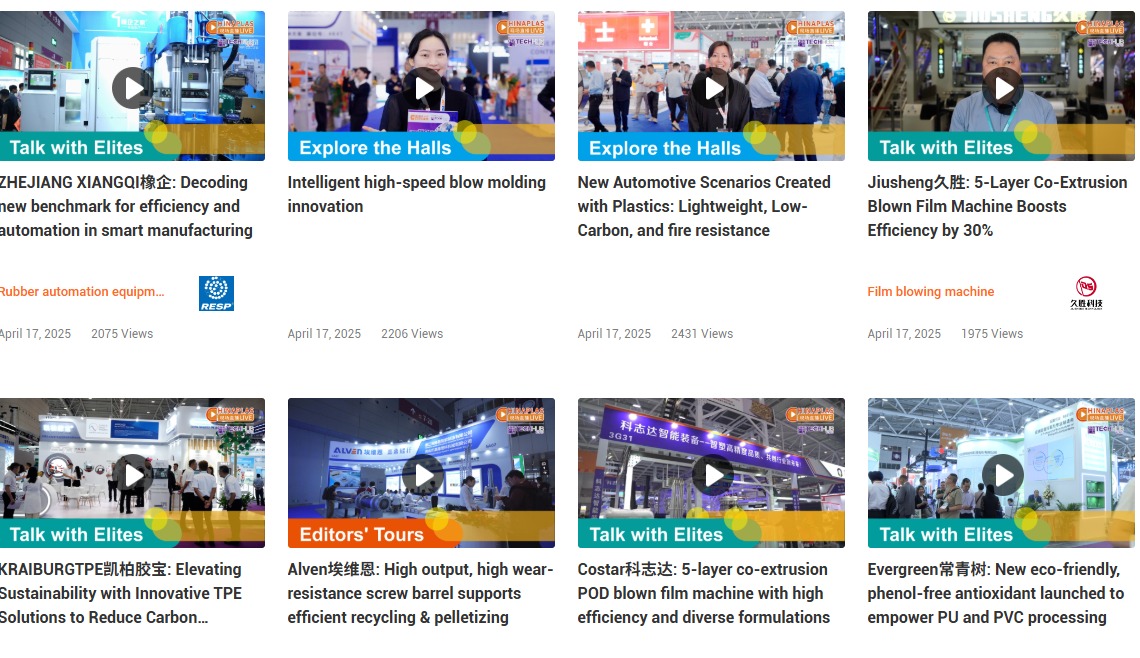
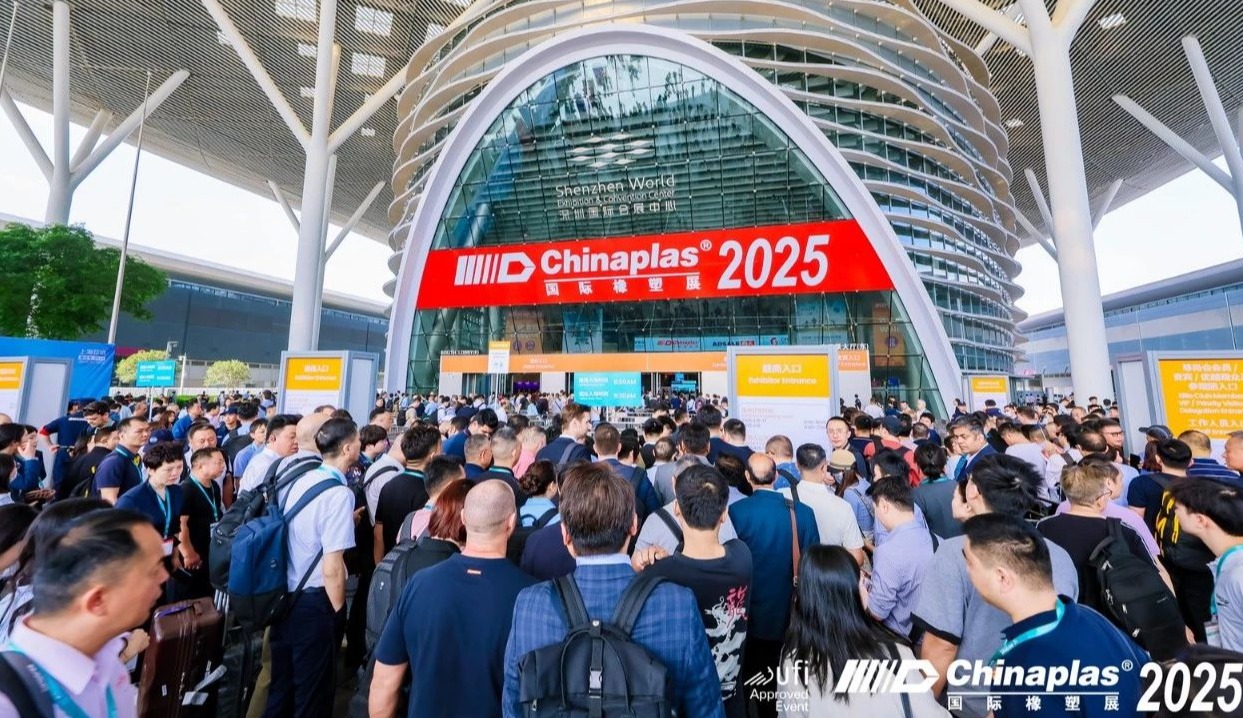
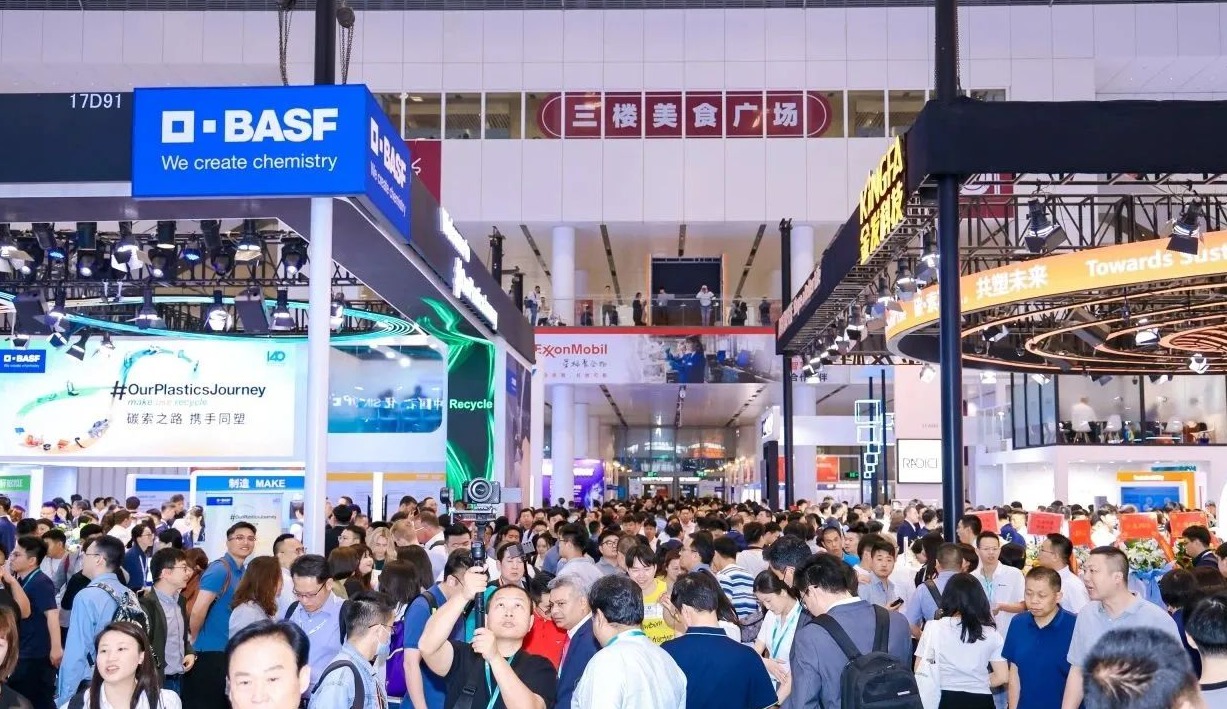
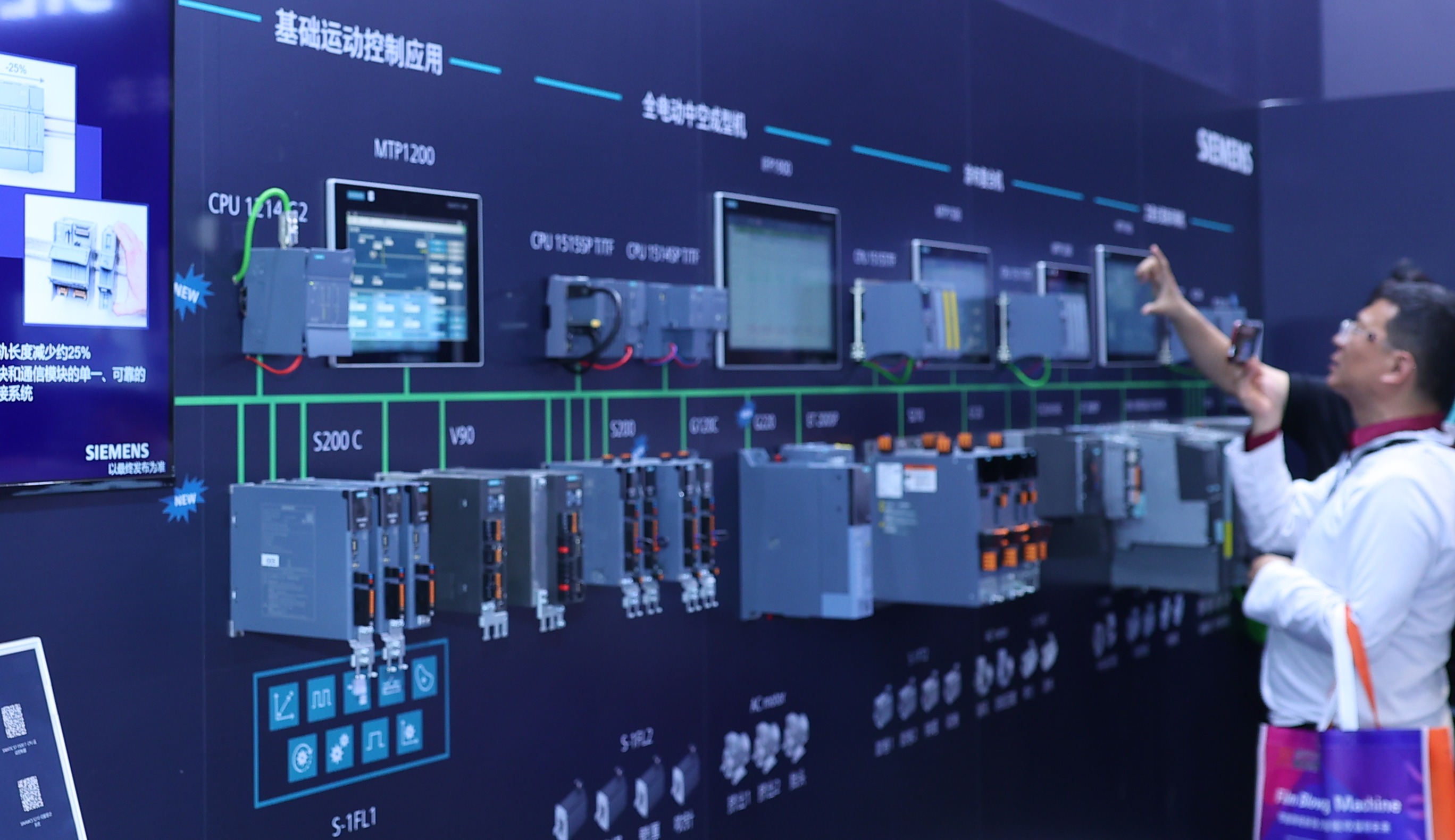
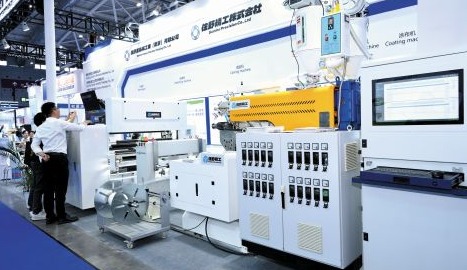
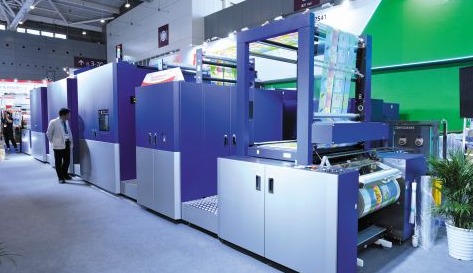
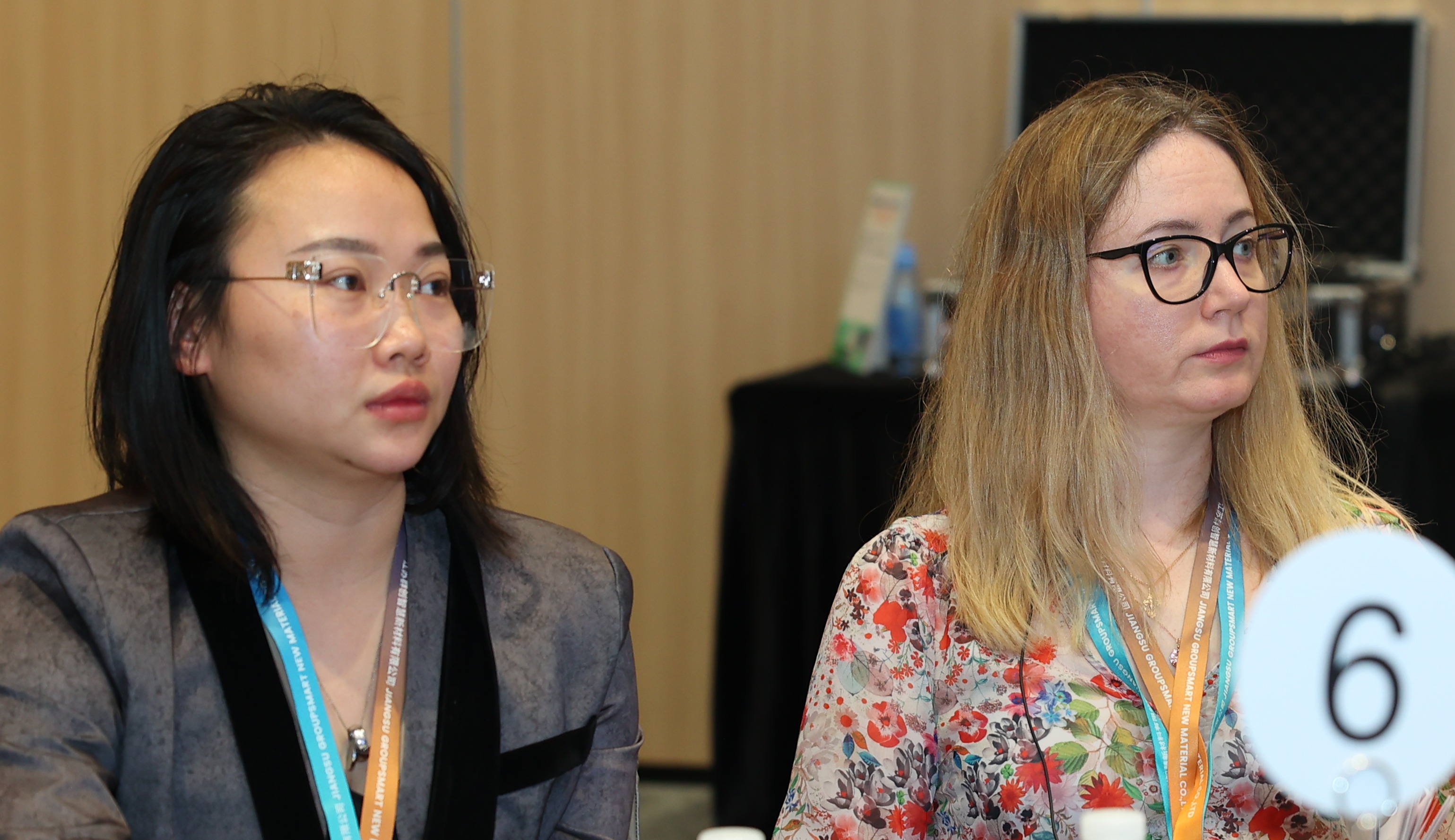
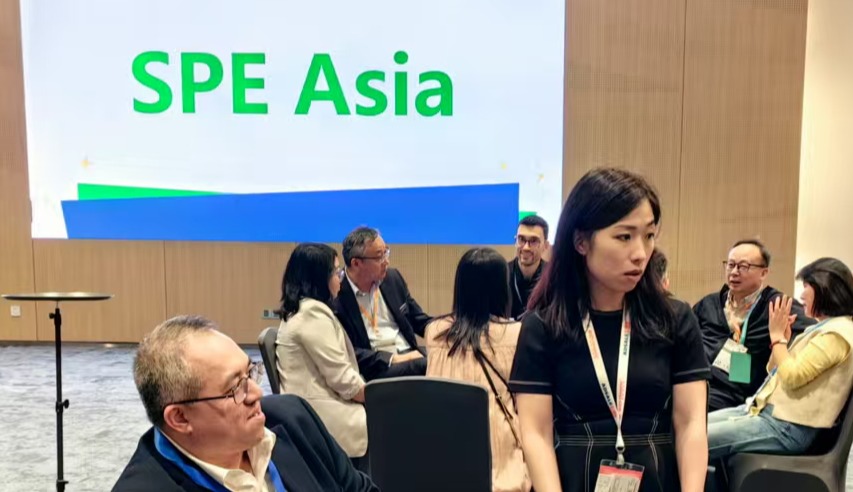
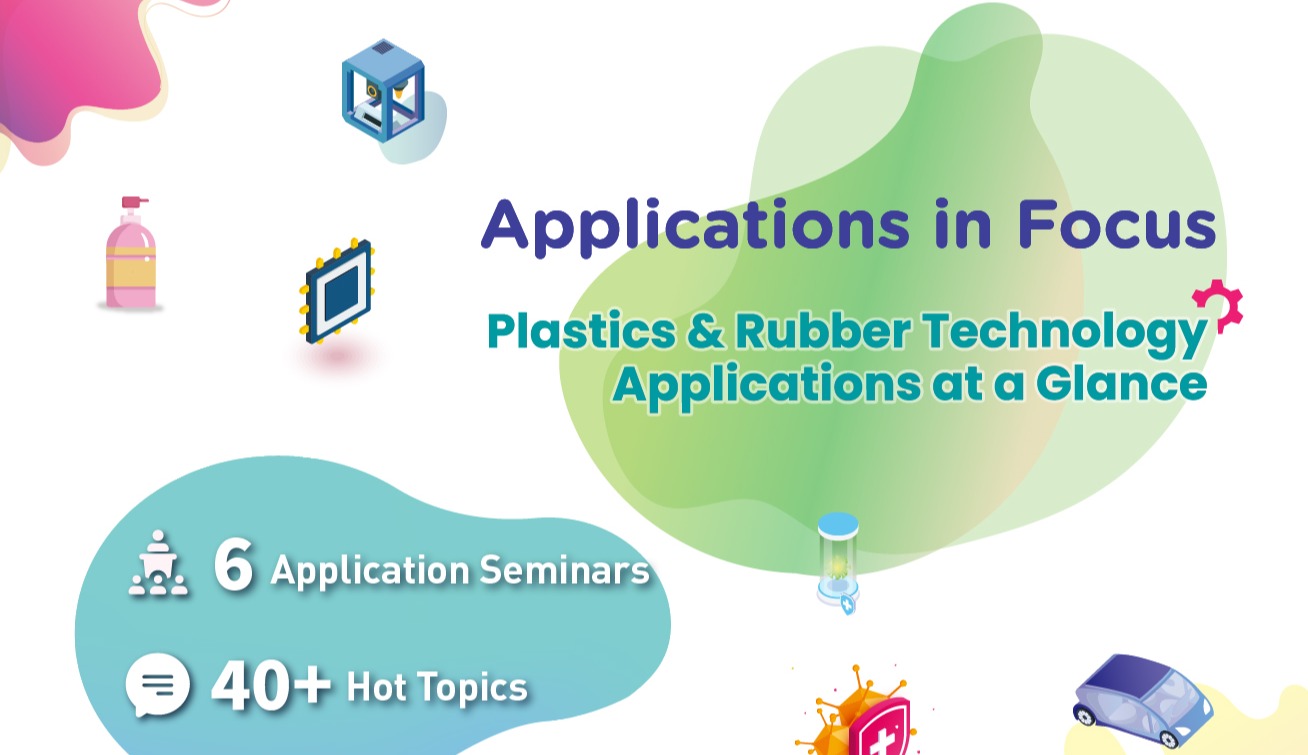
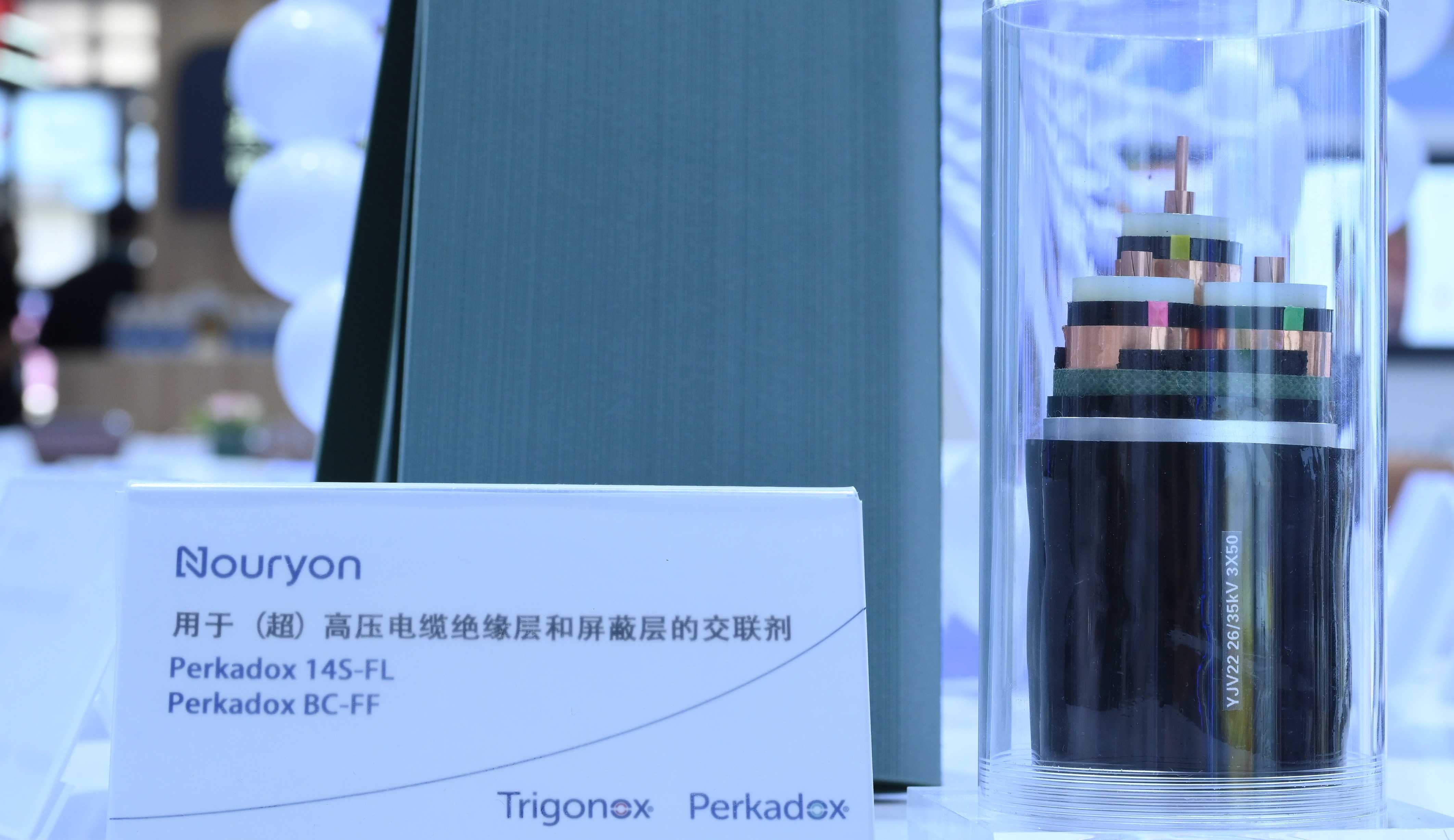
Must See






- Hot Specials
You May Be Interested In

Change
- People
- Company
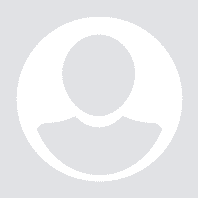
Hot Tags